Introduction | Powertrain Control Software Development
The hardware and software of electric vehicles (EVs) are becoming increasingly complex. As a result, it is essential to have robust and continuous testing systems used in their development, especially for existing EV electronic control units (ECUs). To enable the use of a continuous software testing approach when dealing with EVs, robust modeling and automation solutions are necessary to ensure that tests run seamlessly and provide meaningful results consistently.
ECU code testing is performed before using the actual system, which dramatically reduces the chances of a destructive start test. By porting controller algorithms to real hardware early on, a significant number of issues can be resolved before system integration. As a result, this approach significantly reduces development time and cost.
To make the testing process more realistic, specialized hardware must be employed so we get the testing environment of the ECU as close as possible to the real physical environment. The best option for faster and more accurate testing is to use specialized benches that provide all the necessary testing hardware and multiple connections to plug new devices in and track internal signals. These benches also offer protection for users and ECUs.
Setup | Building the Test Bench
A specialized bench comprises a group of devices connected to enable ECU code testing. These devices are used to:
- Perform the e-Drive simulation.
- Condition signals between HIL and ECU.
- Simulate faults and temperature measurements.
- Insert hardware faults.
The simulator is the central piece when testing ECU software. It will simulate the drivetrain based on a model created by the engineering team. The state-of-the-art solution to perform this task is real-time simulation based on HIL. The Typhoon HIL606, for example, can emulate models with down to 0.2 µs time step, support up to 8 three-phase detailed converter models per device, and provide analog and digital I/O and communication protocol interfaces.
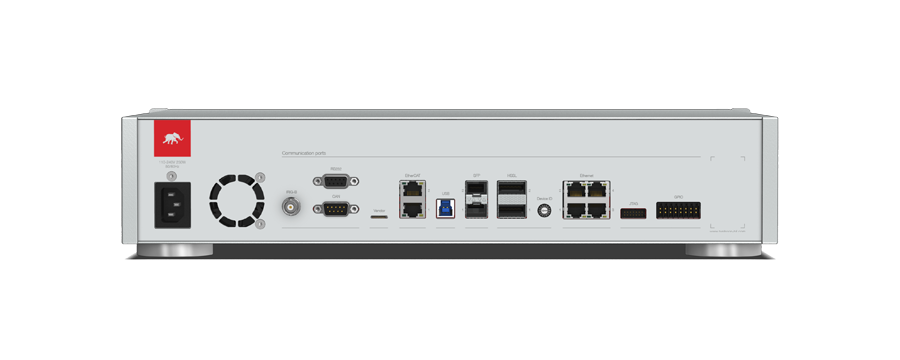
When testing e-Drive ECUs, signals must be conditioned to properly represent what the ECU would be receiving in a real system. To create an environment for the ECU to be tested as close to real-world as possible, certain signals may be outside of the +/-10 V range of the HIL device or may even include resistance values which the ECU converts to temperatures. For these scenarios, the HIL Connect device acts as a signal conditioning device between the HIL and the ECU as well as provides other signal types besides voltage signals.
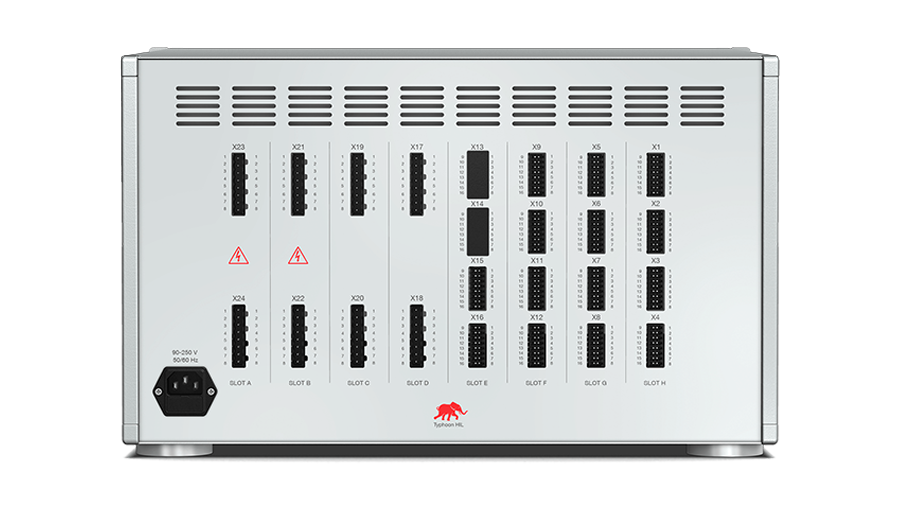
In the context of EVs, ECUs are vulnerable to electrical disturbances due to switching protective devices, passive and active components, and while charging the battery packs. These disturbances can adversely influence ECU safety. To ensure safe operation and replicate a real-world start up/shut down procedures, the signals to (and from) the DUT are passes through relays which can be software triggered to close or open in an orchestrated fashion. Finally, the benches must provide a safe compartment for the ECU, avoiding mechanical impacts and adverse connection issues in case of problems during the test procedures.
In addition to the core hardware, the testing benches require complementary devices to increase the testing fidelity. These devices are used to induce hardware faults and test the measurement capabilities of the ECU control algorithms.
Measurements | Temperature and Faults
When it comes to thoroughly testing ECUs, temperature measurement and fault tests play a critical role in ensuring the reliability and safety of the system. Temperature sensor emulation is done using resistor networks acting as resistance emulators for the ranges that the DUT is expecting to read, while regarding the fault tests, they introduce controlled faults to assess how the system responds to adverse conditions.
You can insert faults in your tests through software using the HIL simulator. However, to represent real world faults more accurately, specialized hardware can be integrated to the testing benches. Fault Insertion Cards are an option designed to be used in the Modular HIL Connect. They use a relay network to simulate fault conditions in a system, such as open circuits, short circuits between input and output terminals, and short circuits to an external signal fed to the fault terminal.
When performing fault or other tests, you may be interested in analyzing ECU signals to understand better how the control works. Accessing signals easily and without creating interferences can be a complex task. However, when using specialized test benches, you can use break-out boxes, which provide convenient access to the desired signal. As a result, you can use banana plugs combined with oscilloscopes or multimeters to analyze signals closely. Depending on the application, you can use break-out boxes with shielded cables to access:
- Noise-sensitive phase current signals.
- Noise-sensitive resolver signals.
- Noise-sensitive inverter gating signals.
- CAN signals.
In addition to faults, it is crucial to test a controller’s response to changes in the operational temperature of devices. In the case of e-Drives, it is essential to ensure that the controller can regulate inverter and motor behavior to maintain their integrity. These temperatures are typically measured using NTC thermistors. Resistor Emulator Cards can be integrated into the bench and controlled via CAN using a HIL simulator to test the ECU.
Modeling & Testing | Advanced Hardware and Software Solutions
For optimal product development, you must have superior hardware and supporting tools. Typhoon HIL offers cutting-edge and sophisticated development tools that reduce design time and costs and ensure that the quality and reliability of your solutions are maintained at the highest levels.
As the development of electric vehicles evolves rapidly and new standards are introduced or updated, it is essential to have software solutions that are easy and flexible to use for effective testing. The first step in testing is to have appropriate models of your EV drivetrain. Although it is possible to model each component from scratch, the modern scenario requires faster solutions. This is where modeling environments with pre-packaged models come into play. Software such as Typhoon HIL’s Schematic Editor provide hundreds of pre-built components, including inverters and batteries, that can be used as building blocks to create simulation systems by simply drag-and-dropping, reducing modeling time.
Once you’ve designed your model and parametrized the components inside the schematic editor, you need to transition the model to real-time operation and create a run-time interaction UI for your simulation. The generated models must be compatible with testing and automotive tools and be prepared for standards evaluation. Furthermore, it is important to have easy ways to interact with and control the testing bench. You can use SCADA software such as the HIL SCADA from Typhoon HIL to accomplish this. Using widgets, you can interact with the simulation models and the testing bench in real-time or inspect the test results.
TyphoonTest IDE is an intuitive graphical user interface that simplifies test creation and automation. It is based on pytest and the Allure framework, and includes a comprehensive API. As a result, you can take advantage of the vast existing testing solution from the Python community, perform actions through your server, and automatically generate reports with interactive test results. In addition, TyphoonTest has a library with a rich set of generic and domain-specific functions that empowers you to build test scenarios, capture signals, apply transformations, and analyze data with minimum coding.
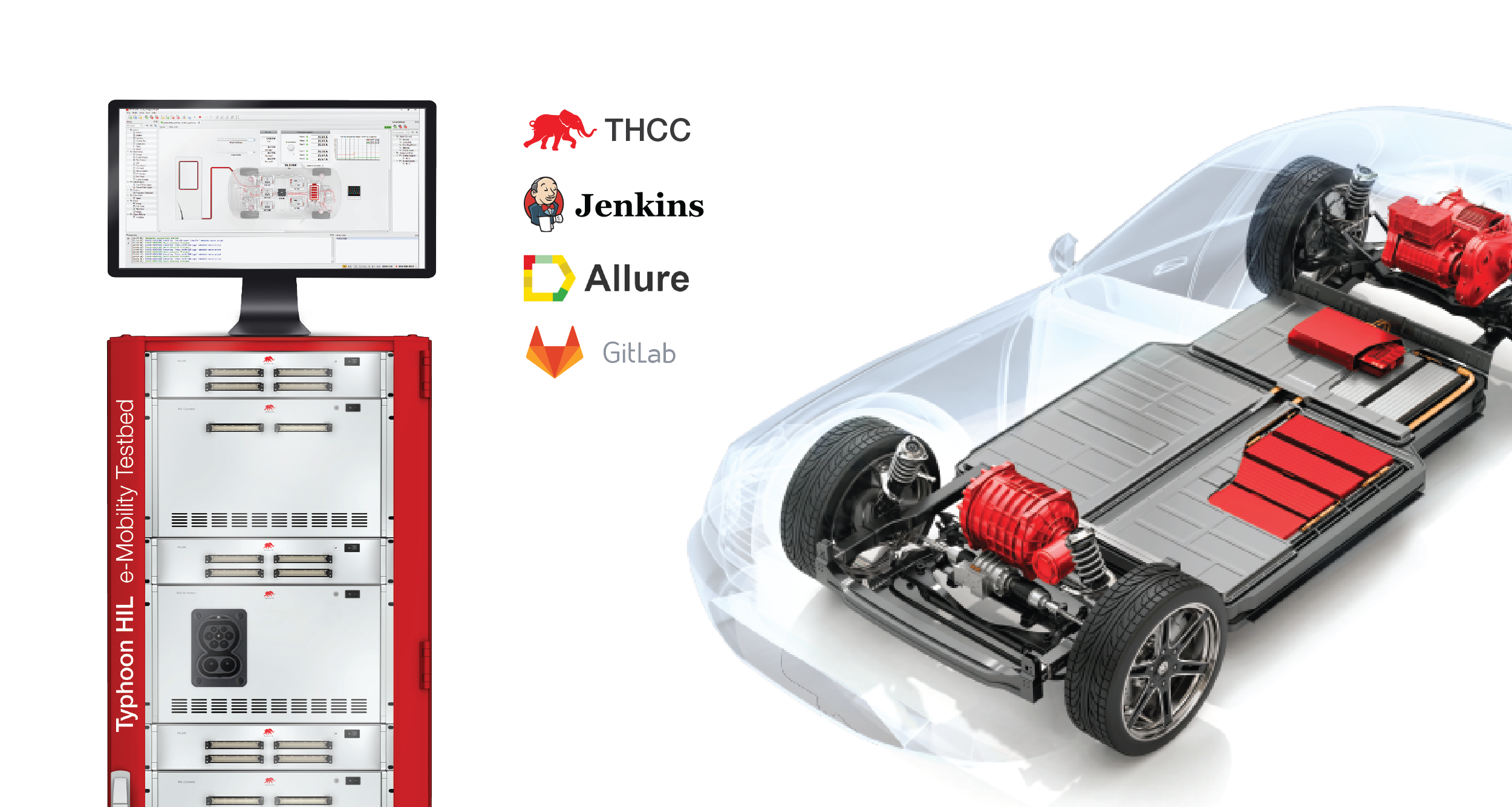
Conclusion | Accelerate e-Mobility Testing
In the rapidly evolving landscape of EVs, ensuring the reliability of ECUs is critical to guarantee the drivers’ safety. Robust and continuous testing, as outlined in this article, offers a future-proof solution to this challenge. Specialized testing benches, real-time simulation, and advanced modeling tools provide a complete approach to ECU testing. With the integration of fault insertion, temperature emulation, and automation, EV developers can streamline their testing processes, reduce development time, and enhance their systems’ overall quality and reliability. As the EV industry advances, these testing methods are set to play a critical role in every development team. Typhoon HIL is here to support you in this journey with the best combination of specialized software and hardware for your testing applications.
Credits:
Authors | Cassiano F. Moraes, Heitor J. Tessaro
Editors | Boris Jovanovic, Petar Gartner, Debora Santo
Visuals | Gustavo Bruinsma, Heitor J Tessaro, Karl Mickei, Milica Obradovic