The Best Just Got Better.
While the automotive and aerospace industries have already adopted model-based HIL testing, the power electronics industry is only playing catch-up. The good news is that the 4th generation HIL is delivering the unprecedented model fidelity needed for the most advanced motor drives and automotive power electronics applications.
High switching frequency converters, new wide-bandgap semiconductors, and new topologies are fueling the need for next-generation controllers that are demanding HIL testing with ever smaller simulation time steps; faster gate drive sampling times; smaller loop-back latencies; and increasing model fidelity (including nonlinearities, spatial harmonics, etc.).
Probably the two most demanding power electronics applications for HIL testing are in the Electric Vehicle (EV) domain, namely: high-performance motor drives, and battery chargers. Such applications pose a significant challenge to real-time simulation fidelity. This is especially true for high switching frequency DC-DC converter applications (e.g. Dual Active Bridge (DAB)) where power transfer is carried out at high frequencies. For some practical applications of this type, even when the time resolution enhancement methods are employed, the 500ns simulation step is simply not good enough leading to prohibitively high simulation errors.
Ultra-high fidelity supercharged.
Our answer to the challenge is the 4th Gen HIL Device, the HIL404, our fastest HIL machine yet. With its ability to reach simulation time steps down to 200ns combined with an input sampling resolution of 3.5 ns it pushes the high-fidelity real-time simulation into a whole new dimension.
To illustrate some of the benefits of HIL404, we did a comparative analysis of the relative power errors between the HIL402 and the HIL404 for a Dual Active Bridge (DAB) application. The model is controlled by an external open-loop controller switching at 100 kHz and with a dead time of 50 ns. Power transfer is measured and compared against the analytical model for a given phase shift. The error is mainly caused by the limited time resolution of the simulator. Here we can clearly see the benefits of the 2.5 times smaller simulation time step and higher frequency sampling provided by the HIL404.
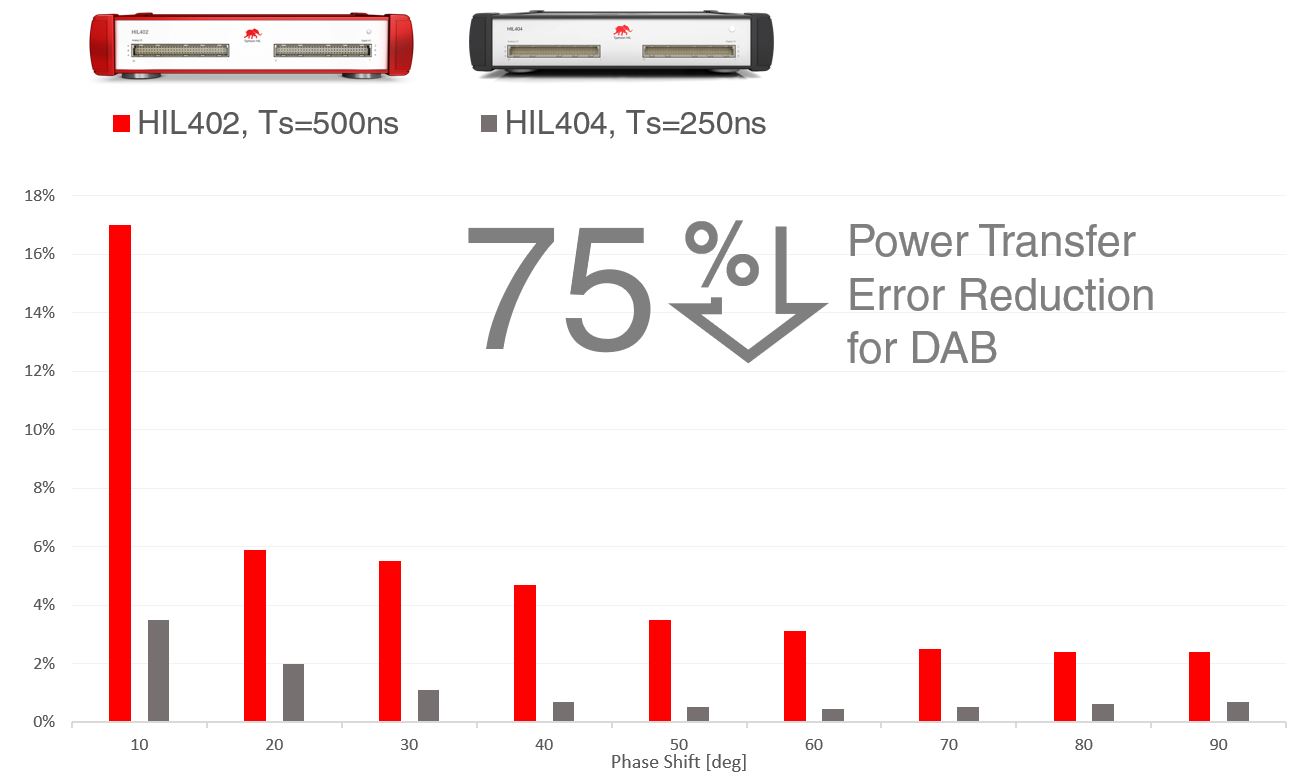
Advanced electric machine models. One click away.
However, HIL404 is so much more than just a faster HIL402 tuned for very high frequency applications. It is a device that brings many advanced features of our industrial grade 6-series devices to the 4-series, such as:
- Nonlinear machine modeling;
- Accurate real-time converter power loss calculation; and
- Extended connectivity with out-of-the-box support for CAN, RS232, USB 3.0, and ETH protocols, including device paralleling support.
Indeed, HIL 404 supports the direct import of high-fidelity JMAG-RT electric motor models directly obtained from JMAG’s Finite Element models (FEM). With one click the nonlinear and spatially varying inductance FEM derived models run in real-time with unprecedented fidelity.
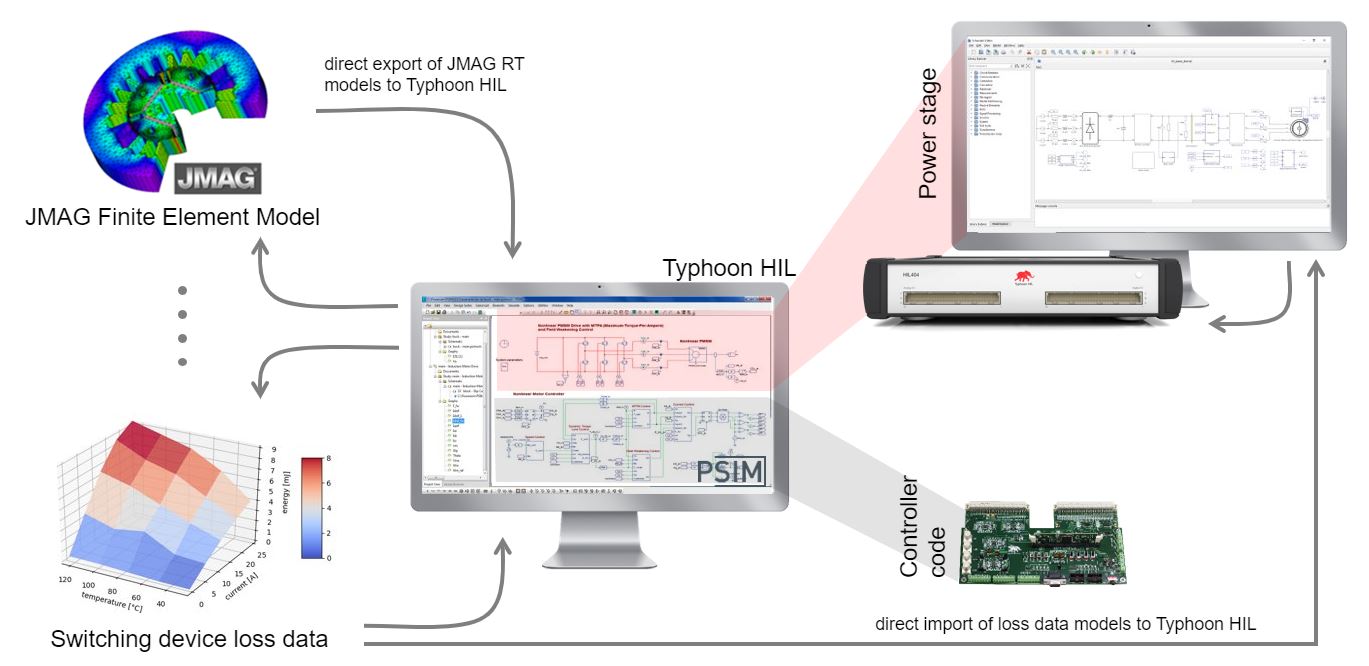
In addition, HIL404 supports one-click import of power semiconductor switching and conduction losses directly from datasheet look-up tables. It has never been so easy to run high-fidelity and accurate thermal models in real time.
By leveraging the ultra-high fidelity and ease of use of the existing Typhoon HIL solution, and by bringing the extra speed to the table, the HIL404 makes the HIL testing methodology truly applicable to emerging high-frequency power conversion applications.
Credits
Author | Dusan Majstorovic
Visuals | Typhoon HIL
Editor | Debora Santo