Introduction
Industry 4.0 is dawning, and digitalization, decarbonization, and decentralization (aka D3) are fueling the electric grid (r)evolution. D3, in turn, creates opportunities for immense value creation, but invokes new technologies and design concepts, and change brings risk.
The emerging cyber-physical grid â with proliferating distributed energy resources (PV, wind, gensets, batteries, etc.); embedded controllers; intelligent sensors; communication links; large data; multilayered distributed digital control; and cloud software â is forcing industry leaders to embrace new design, test, deployment and lifecycle maintenance tools and processes.
Twentieth-century power systems incorporated the physics of electro-mechanical systems â dominated by inductive generators, motors, and transformers â which eventually grew into the synchronized grid that has been called the worldâs largest machine. Cyber-physical systems bring not only dramatic increases in data but fundamentally different power devices. The inverters, power converters, and motor drives that are being installed in homes, infrastructure, and factories today utilize rapid digital electronic power switching to manipulate currents, voltages, frequency, and other attributes as needed. Their flexibility delivers a dramatic increase in possible system behaviors and interactions that cannot be adequately analyzed with classical engineering tools. Model-based methods, such as Controller Hardware in the Loop (C-HIL) tools, are beginning to supercharge power electronics and microgrid design as well as deployment processes.
HIL testing has been a standard in the aerospace industry for decades; from testing jet engine controller units, all the way to the autopilot. The safety criticality of airplane control systems set the bar high in terms of control software development, testing, and maintenance processes. For example, no jet engine controller gets flight certified without an extensive record of HIL testing, in addition to regular laboratory testing and a significant number of flight hours. HIL testing has become a ubiquitous tool to maximize test coverage, reduce per-test cost, and achieve requisite reliability in aerospace.
As high-performance modeling and simulation tools become more affordable, microgrids stand next in line. Most equipment vendors have adopted HIL testing, and microgrid system integrators are beginning to use its extensive testing and validation capability to characterize and validate microgrid control system performance, integrated with DERs and smart devices, to assure performance, reliability, and cyber security. A HIL Tested environment provides the ability to virtually test firmware and software in a safe, repeatable, and systematic way as the system is being developed, rather than waiting until after startup.
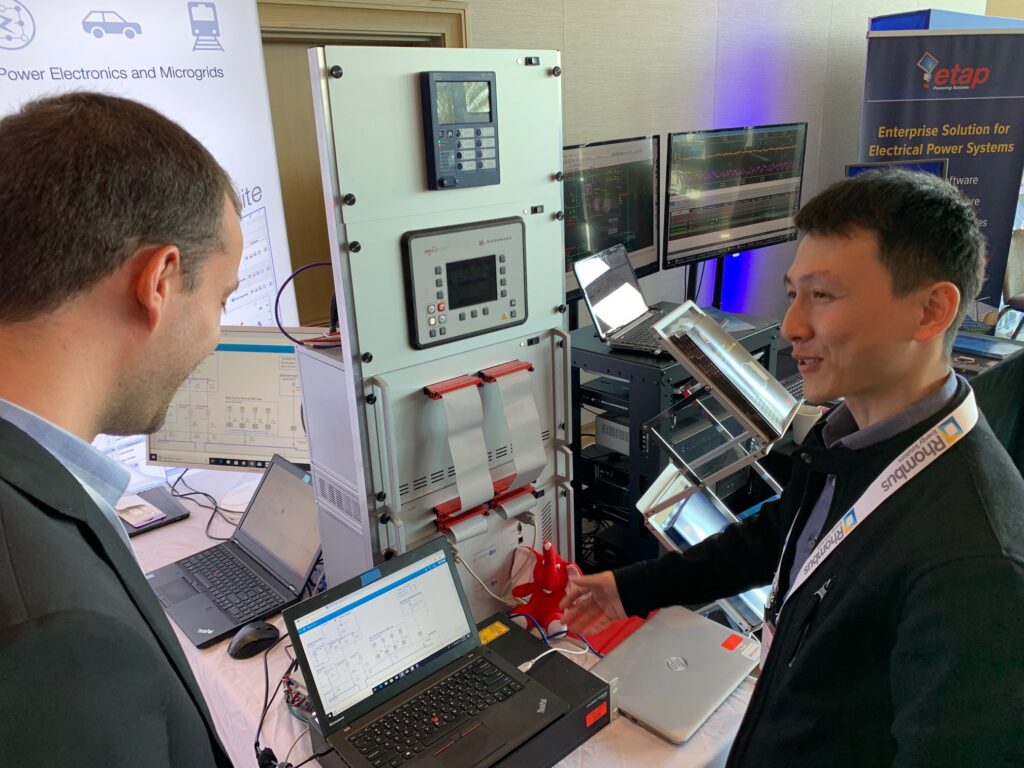
Here are four ways Controller Hardware in the Loop (C-HIL) and model-based engineering can reduce the risk during the design, deployment, and operation of your microgrid:
1. Manage control complexity and guarantee interoperability.
Over the past 30 years, embedded systems have undergone exponential growth in control code complexity as measured by the number of Source Lines Of Code (SLOC). To illustrate this trend, consider three examples:
- F-35 fighter plane code grew from 6.8M (SLOC) in 2006 to 24M (SLOC) in 2013
- Automobile (high end): from 2M (SLOC) in 2000 to 100M (SLOC) in 2018
- PV inverter: from 0.05M (SLOC) to 0.2 (SLOC) in 2018
As smart inverters and other cyber-physical components grow in sophistication, their programming complexity climbs a similar exponential curve. Even today, a typical microgrid with 10 smart inverters, 10 protective relays, and one microgrid controller can easily reach 5 million of combined SLOC. When we network hundreds of microgrids in virtual power plants or similar system architectures, we will soon reach scales that exceed a billion SLOC.
Indeed, the exponential increase in code base will transform microgrids and utilities into truly flexible, multi-functional, and adaptive (resilient) cyber-physical systems. Clearly, we need the right tools and processes to support and accelerate this transformation.
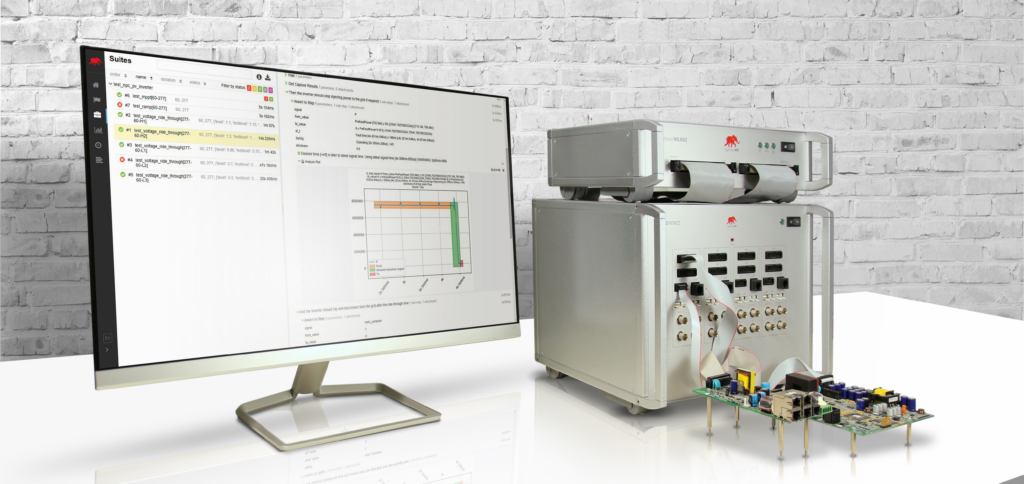
Increasing test coverage and reducing your development times without compromising the quality of the firmware are quality aspects that we feel HIL tested would add to our portfolio of products.
Sau Ngosi
CTO Residential Solar & Storage
Schneider Electric
How does one maintain and improve microgrid control software quality while managing exponential growth in complexity? It is simple, but not easy. The aerospace and automotive industries have demonstrated the value of religious Hardware in the Loop, model-based testing; continuous integration (CI) software development processes; broadly-based development testing; and test automation. VDC Research results show a 38 % reduction in the number of software bugs when Controller Hardware in the Loop (C-HIL) is used early on in the design process and throughout the lifecycle, including a 60% reduction in the cost of fixing bugs when embedded software is developed and tested using the C-HIL methodology.
2. Reduce time to market and innovate with confidence.
Traditionally, power electronics and power systems industries have been slow to introduce new products and new functionalities. Limited lab testing and operational field experience provided the only feedback; mistakes were costly. The approach âif it works donât change anythingâ led to product design cycles of 5+ years, and product lifecycles could be greater than 25 years.
HIL Testing is flipping this paradigm upside down and is empowering developers to continuously improve and integrate new functionalities by easily adding new software functions. As product changes and upgrades increasingly become software-based, better code processes can accelerate innovation. Consider the example of a Tesla car. With remote updates, the owner often wakes up to a different car in the morning â one with new functionality and better performance. In the future, microgrids will be upgraded and improved in the same way, with new software that was thoroughly tested using a C-HIL testbed under tens of thousands of test scenarios.
Our system integrator Raytheon extensively used a Controller Hardware in the Loop (C-HIL) testbed during the design and development phases – before the Microgrid was even built – to test and validate a spectrum of operational scenarios, including fault conditions. This significantly reduced interoperability risk.
Shawn Doyle
Otis Air National Guard Base, Massachusetts
Raytheon
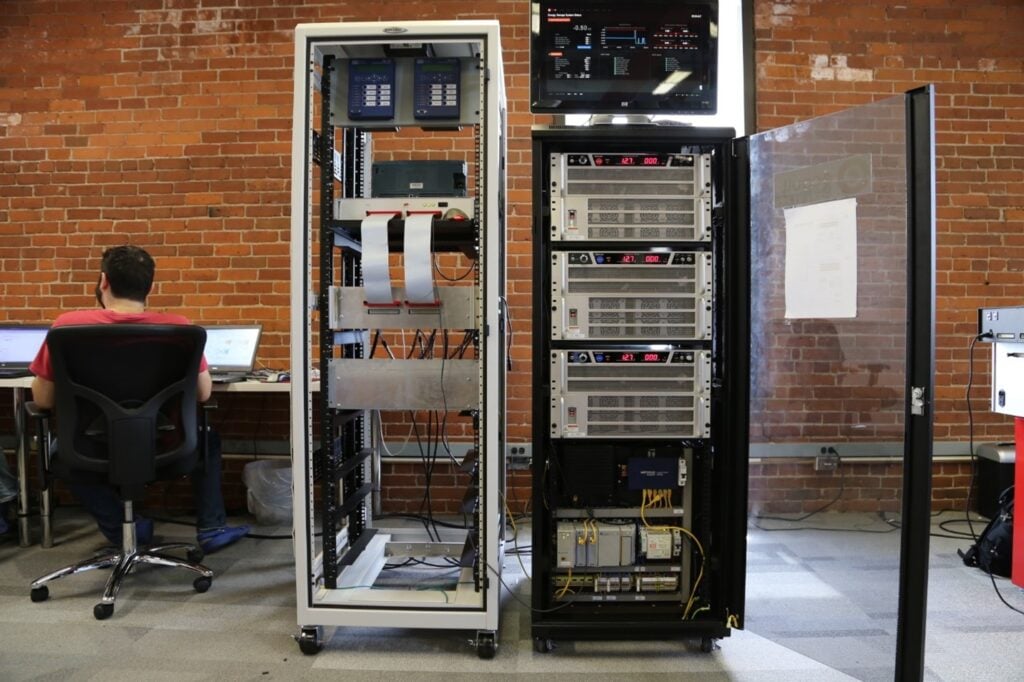
Otis Air National Guard Base (ANGB) Microgrid. DoDâs first cyber-secure controller with an outside connection and the first wind-based DoD microgrid were tested and validated with Typhoon HILâs ultra-high fidelity C-HIL testbed.
3. Empower system integrators.
Today, most microgrid projects are brownfields or modifications to existing infrastructure. Brownfield projects require system integrators to gracefully orchestrate old and new equipment, interfacing new control and communication infrastructure with existing assets; upgrading existing DERs; and integrating new microgrid controllers with the distribution system operation.
We will provide the model of our system, and then other people – a third-party, our customers or a system integrator – would use our model integrated into their system model, so now they can simulate the entire system.
Nicolas LaRue
Global Offer Manager
Schneider Electric
C-HIL and model-based engineering enable system integrators to prototype the composite system with full fidelity, early on in the design phase, and use the developed model to test and validate microgrid design every step of the way.
HIL is starting to change our relationships with our customers. We are providing access to the Hardware-in-the-Loop system to them, and thatâs helping them understand the operation of the inverter better and allows them to answer some of their own questions about capabilities, operational sequencing, etc.
Ryan Smith
Chief Technology Officer
EPC Power
4. Supercharge life-cycle maintenance with a C-HIL Digital Twin.
Much of todayâs focus is on winning the project, followed by design and commissioning. Like all infrastructure, however, microgrid lifecycle operation and maintenance is of critical importance to investors, users, and operators, but is rarely given serious consideration upfront. A C-HIL testbed, or a very high-fidelity microgrid Digital Twin, can provide an opportune environment to:
- Seamlessly test firmware and software upgrades to smart devices and microgrid controllers before deployment;
- Model and simulate anomalies that may be anticipated or discovered during operation, and test fixes;
- Test equipment upgrades and any interoperability issues that might arise before deployment.
Indeed, a C-HIL testbed provides a high-fidelity model of the as-built microgrid that can be maintained and upgraded as the microgrid evolves.
Our project will require testing and refinement overtime. Even now, as we prepare for commissioning, we are anticipating micro outages and frequency anomalies in the grid that might âupsetâ our system controller. Having the Digital Twin in the form of the C-HIL testbed will enable recreating these events in the C-HIL Digital Twin and troubleshooting and optimizing these issues without the concern of damaging equipment or having outages onsite.
Shawn Doyle
Otis Air National Guard Base, Massachusetts
Raytheon
This represents the new standard for risk reduction in the Twenty-first Century power system development and maintenance.
Credits
Author | Ivan Celanovic
Visuals | Typhoon HIL
Editor | Debora Santo