Marine Power Systems
Marine Power Systems (MPS) are complex networks of many interconnected components. Ensuring their long-term reliability, especially amidst unpredictable maritime conditions, hinges on precise maintenance and preemptive solutions. Advancements in technology and engineering are illuminating blind spots, mitigating the need for costly and inefficient sea trials that could result in equipment damage or dangerous conditions.
Typhoon HIL addresses these challenges with our vertically integrated Controller Hardware-in-the-Loop (C-HIL) solutions – a comprehensive alternative that mirrors the performance and behavior of Marine Power Systems. By incorporating physical hardware components, such as generator controllers, system controllers, and protective devices, into the software simulation loop, our HIL’s provide reliable and comprehensive testing environments that mimic real-world conditions. With HIL testing, you will never have to fear sea trials for shipboard electrical systems.
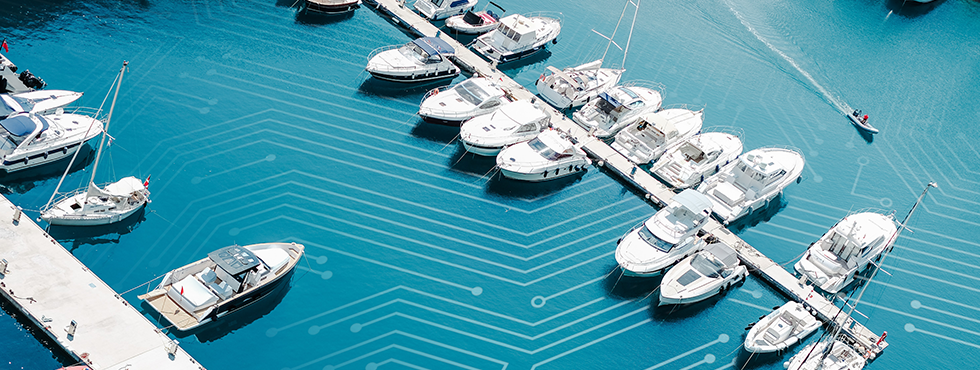
Eradicate Interoperability Issues
Shipboard Power Systems (SPS) must be tested under all operating conditions to ensure safety and functionality. Any issues occurring during operation can be easily recreated, understood, and solved in the virtual environment. Validated modifications can then be made on the vessel itself. Digitalized during design or while in operation, detailed digital replicas of all vessels in your fleet are stored and easily reachable for future retrofits and firmware updates. By integrating complex control systems with a high-fidelity digital replica of the shipboard power system, engineers can fully solve Marine Power Systems interoperability issues while the ship itself is still being built or being improved.
Typhoon HIL helps you:
- Stress-test and validate the entire systems in a virtual environment for pre-emptive emergency scenarios
- Create a fully working SPS control prototype and assess its behavior at any phase the lifecycle
- Validate component performance before any investments have been made
- Test-drive components of different vendors within the digital twin of your SPS before investment
- Drive your decisions with data, pre-qualify your vendors, and optimize your choice with the price-to-quality balance that matches your needs
- Enter commissioning with confidence and eliminate penalties from extending deadlines
- Leverage the intuitive graphical user interface (GUI) to experiment and find the optimal configurable components
Enhance the stability and resilience of your marine power system and eliminate guesswork with Typhoon HIL solutions.
Marine Microgrid Testbed | Demo
This demonstration features a controller hardware-in-the-loop (HIL) simulation of a marine microgrid on a Typhoon HIL testbed. The featured controllers and protection relays include a Woodward easYgen-3000XT Diesel Genset controller, a SEL-751 protective relay, a Schneider Electric AccuSine active filter controller, and an EPC Power battery inverter controller.