Introduction: AVL’s role in control software testing.
AVL is the world’s largest independent company for the development, simulation, testing, and integration of powertrain systems in the automotive industry. The AVL e-Storage BTE System product line is created and optimized for characterization and verification of electric driveline components for automotive, off-highway, marine, aviation, and stationary power applications. The e-Storage System offers a dynamic and stable bi-directional DC power supply which can act as a battery tester or a battery emulator. When paired with automation systems, it can enable a wide testing range, from single components (electric drives, inverters, batteries, fuel cells, supercapacitors) to complete electrified powertrain systems.
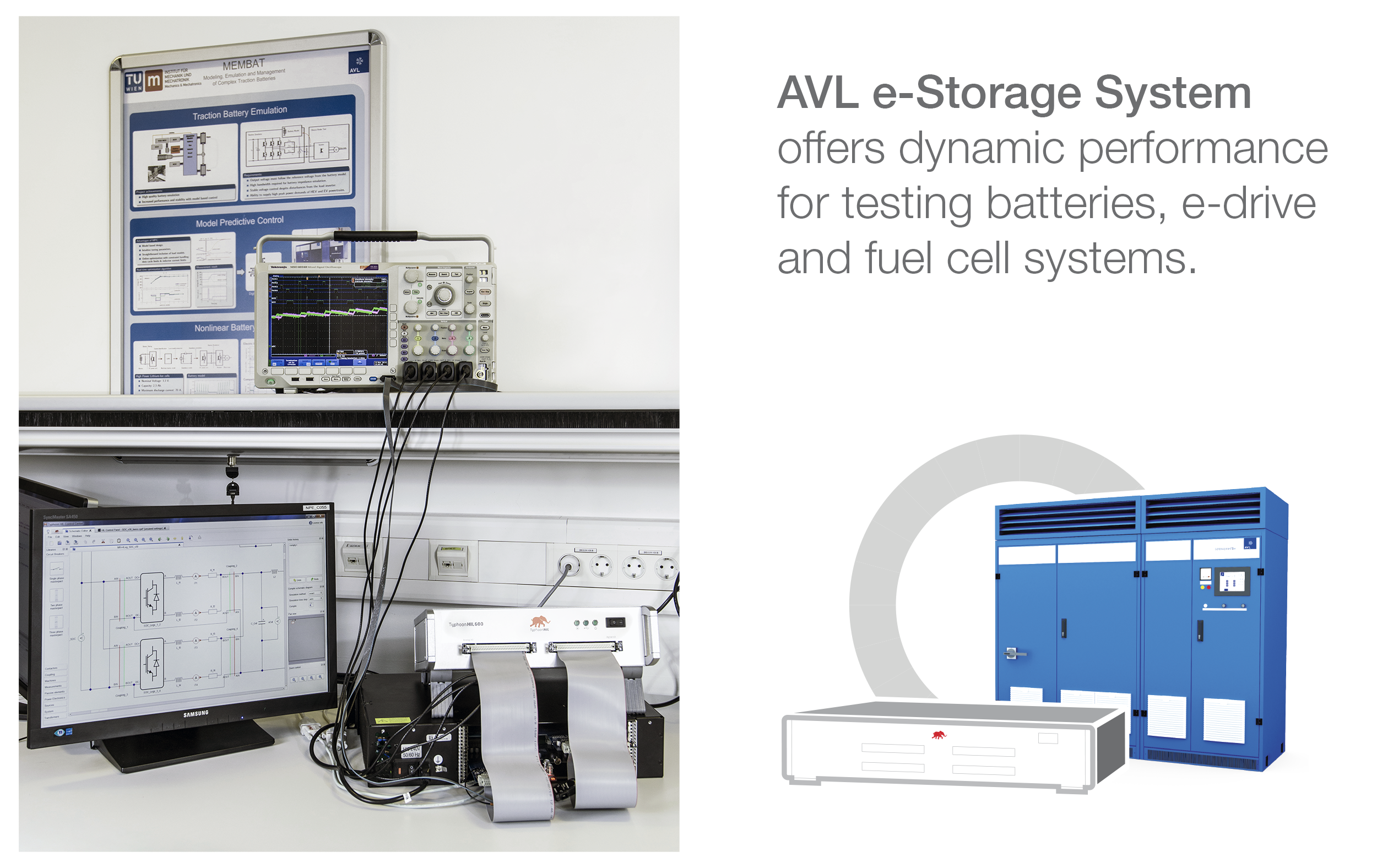
Due to its modular and expandable build, the e-Storage System can be adapted to meet customer-specific requirements. It is characterized by dynamic performance, accuracy, broad voltage range, and stability, with a possibility to follow predefined load profiles. This allows emulation that can expose the devices under test to real operating conditions and demonstrate their behavior in different possible scenarios.
Owing to the ability to port the controller algorithm early to the real target hardware, a large number of issues—especially in control hardware configuration—can be resolved prior to system integration. This results in significant development time and cost savings.
Dr. Roland Greul
BU Electrification and Racing Test Systems
AVL List, Graz, Austria
HIL design and testing play an important role in introducing leading-edge control strategies to new e-Storage product generations. AVL adopted the agile controller development process, completely automated firmware testing, and firmware regression testing, and developed thousands of automated test cases using Typhoon HIL’s C-HIL technology. This approach to firmware testing helped R&D teams reduce control algorithm development and software verification times and efforts, which in turn sped up the time to market for new features and products. In addition, thanks to the capability of the HIL testbed to emulate any of the devices, and in parallel operation as well, the investment costs for keeping a device variant in stock have been significantly reduced as well.
Challenges: HIL testing the test equipment firmware.
Based on intended applications, we understood that the AVL e-Storage BTE system had to satisfy criteria such as high dynamics, broad voltage range (typically 8-800 V), low residual ripple, and stability despite the variety of possible loads. The system is also designed to satisfy different use cases, acting as a battery tester, battery emulator, or electric motor inverter tester. This variability and real-time fail-safe operation depend on the implementation of specialized microcontrollers for digital control of power electronics systems which need to be thoroughly tested and verified.
In order to fulfill the described requirements, the development and test engineer teams had to work on three key system elements simultaneously: scalable hardware design, reliable application software, and advanced control strategy, the last being the most challenging. Accounting for parasitic effects and nonlinearities was not enough; the implementation of the embedded control system into hardware required a development and testing environment where the switching behavior could be observed and analyzed in real-time.
Solution: Embedded software development with HIL.
To ensure prompt verification of the embedded control software, HIL testing was implemented using Typhoon HIL’s 6 series real-time simulation devices at its core. The HIL testbed in use comprises of 4 HIL604 units coupled with the Industrial Premium Toolbox Package, and the TyTest Toolbox for setting up automated test scripts. The computational power and behavior of the microcontroller within the power controller unit (PCU) is evaluated through simple interfacing with the HIL system via an adaptor board. This setup is used for rapid control prototyping (RCP), software regression testing, as well as automated testing of the complete firmware and its variants across all devices, including parallel operation and safety tests.
Relying on HIL testing enables not only closed-loop control verification but also application software testing and debugging from the earliest stages of its development. This is important because it makes it easier to spot and fix errors early on. For this reason, software development with HIL is not only faster but cheaper and safer as well, as the typical costs and potential damages of working with real hardware are avoided. The HIL system can also be used the other way around. The flexible evaluation of the software on simulated hardware in various conditions makes it easier to find the optimal hardware configuration for the desired performance requirements.
The fidelity of these tests is so high that the measurements obtained from hardware prototype setups almost perfectly match data from HIL simulations. Altogether, C-HIL serves as a tool that supports multiple elements of the final product (embedded software, application software, and hardware) throughout the entire V-curve of model-based system development, including system specification, design, prototyping, testing, verification, and even maintenance. While maintenance can often be overlooked, having digital copies of embedded software, hardware, and automated test scripts for a product family like e-Storage System makes project documentation and system maintenance a breeze.
Conclusion: HIL speeds up control software development and verification.
Using HIL test-driven design, the efficiency of product development can be improved in multiple stages of product maturity levels throughout all stages of the product development V-curve. When developing embedded control software for power electronics products, HIL platforms are particularly beneficial as it allows rapid control prototyping to be done in parallel with application software and hardware development. This means control software can now be validated, ported onto real control hardware, and behavior tested to find the optimal configuration prior to system integration. All this results in speeding up the development processes while making them cheaper and safer at the same time.