Introduction | Could you tell us a bit about LS Electric?
At present, we are the number one company in Korea in regards to power and automation that are based on quality assurance and innovation. Our company is already established in the fields of power generation, energy storage, and renewables, while we are the first Korean company to enter the high-voltage, direct current (HVDC) market as well.
In line with LS Electric’s mission of ‘Futuring Smart Energy,’ we are striving to become a company that can lead the global market in the field of smart energy, power systems products and automation technology.
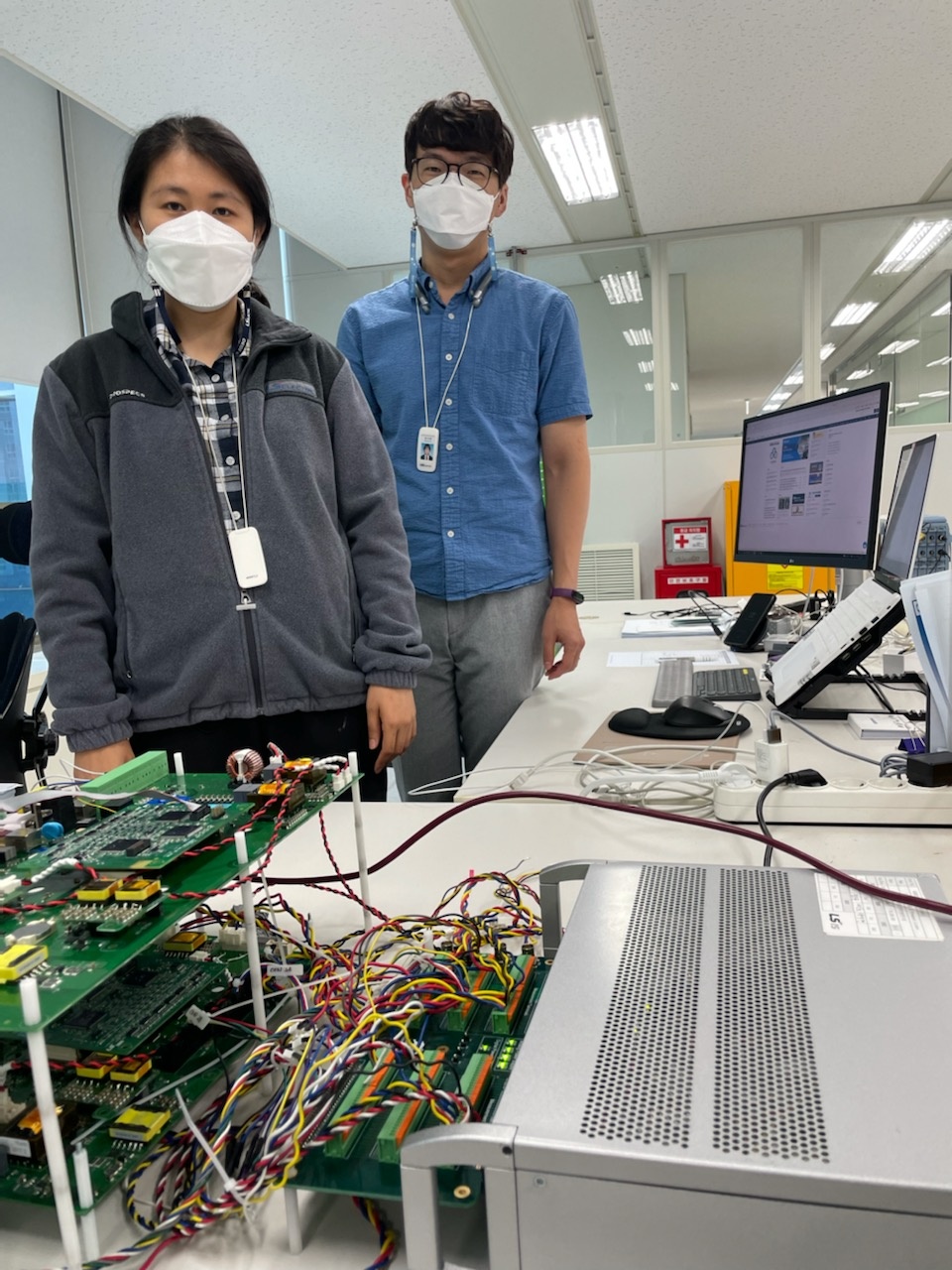
Application | Which team are you a part of and what is the focus of your work?
We are a part of the power electronics research and development team, and our focus is on power converters. Our main products are ESS, Uninterruptible Power Supplies (UPS), and P-STACOM.
Challenges | What are usually the biggest challenges in your domain of work?
Control | Currently, our work is in developing robust controllers, needed for the parallel operation of 15 PEBBs. When designing and verifying controllers such as these, it took us a lot of time to verify in offline simulation, even when working on high-performance computers. The challenge here was to find a way to speed up testing and shorten the product’s time to market.
Communication | Besides testing controller performance, we also require fast and reliable communication verification, as we need 15 PEBBs to communicate efficiently to perform well in parallel operations. It can be a challenge to find a test system that provides communication testing in the same environment as real power converter operations testing.
Certification | The UL1741SA standard requires various tests to be completed for certification purposes before a product can enter the market. Since there are many test cases, it takes a lot of time to verify the functions, and it takes a lot of money to perform all the experiments and to get approval from certification bodies. Failing just one test may result in having to repeat the entire certification from the beginning and pay for it again.
Solution | How did Typhoon HIL help you in dealing with these challenges?
Control | Using the Typhoon HIL solution’s real-time verification on a microsecond time-step scale, we were able to verify our high-speed controller for multiple PEBB operations with the aim of increasing the efficiency, reliability, and longevity of the system. The existing support for the 3-level IGBT library within the Typhoon environment made it easy for us to carry out a systemic implementation. With one Typhoon HIL602 simulator, we were able to verify up to 2 PEBBs. Furthermore, by parallelling multiple real-time simulators to work as one (HIL602 or HIL604 6-series devices), we achieved verification of 3 or more PEBBs as well.
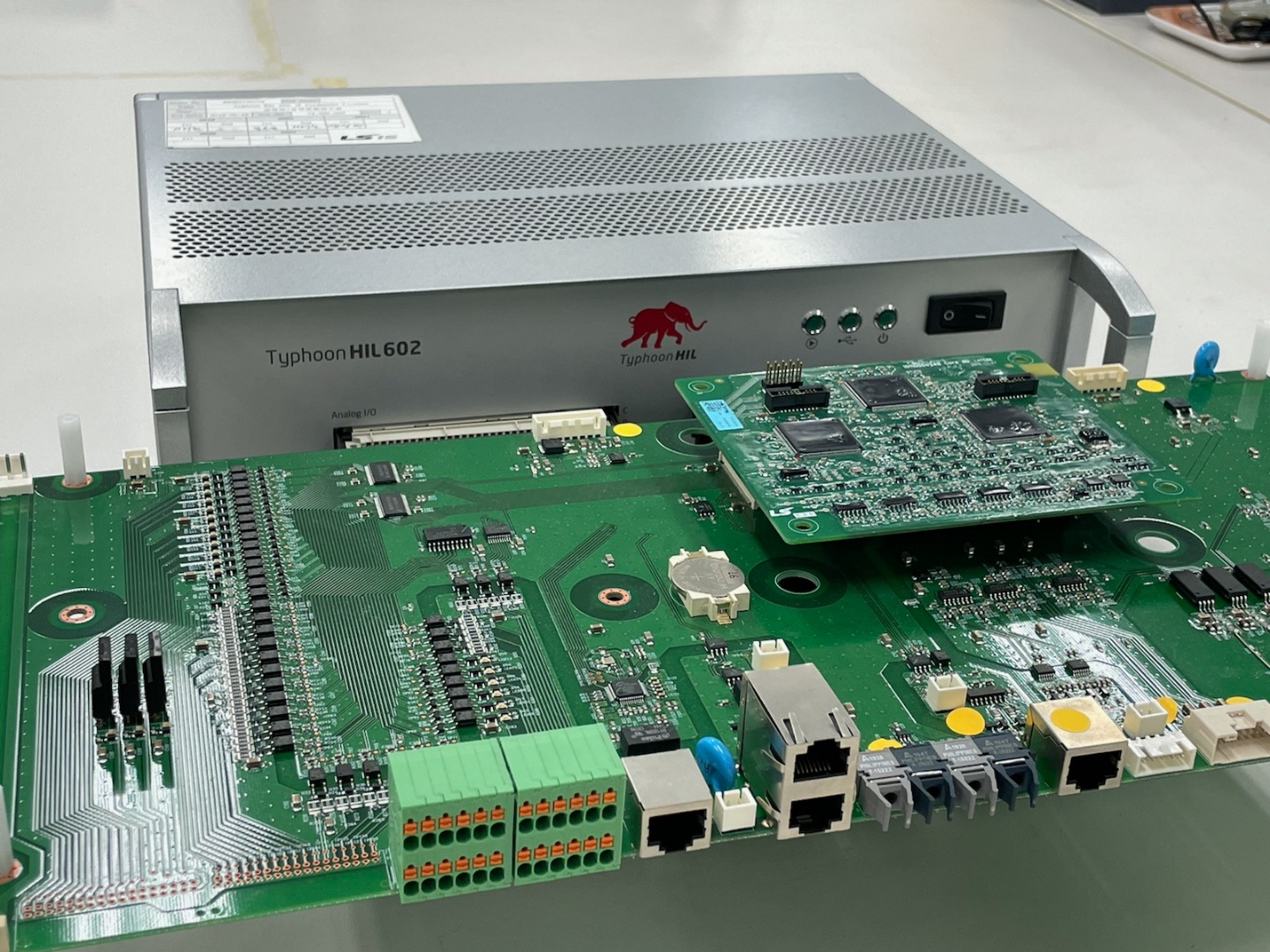
Communication | HIL devices enabled communication testing in almost the same environment as real power converter operations, which improved our reliability in the verification of communication performance.
Certification | UL1741SA certification includes hundreds of tests, the most important being Anti-Islanding, Low and High Voltage Ride-Through (LVRT and HVRT), Low and High-Frequency Ride-Through (LFRT and HFRT), Ramp Rate/Soft Start, Specified Power Factor, Volt/VAr Mode (Q(V)), Frequency-Watt (FW), and Volt-Watt. Using Typhoon Test IDE for implementation and verification of several grid support functions using scripted Python test automation, we were able to reduce time and money for certification. The possibility to approach certification with internal pre-certification already conducted gave us confidence that the certification process will be passed successfully without additional costs.
Results | What were the main deliverables of this project?
Thanks to the real-time power electronics simulation technique provided within the Typhoon HIL solution, we applied a 3-level topology where up to 15 PEBB blocks can be operated in parallel. The concept of the Modular Scalable Platform enabled customized capacity selection and introduced advanced optimal driving techniques. Each PEBB can be operated independently, improving system flexibility and adaptability, while a master control optimizes the entire system’s efficiency and longevity.
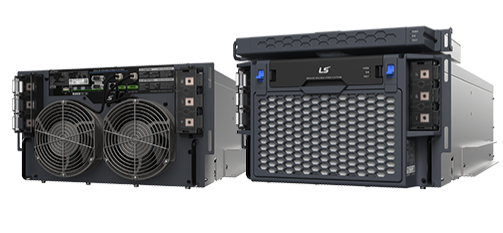
The smart power solution we developed is as a result powerful, flexible, and reliable. Its modularity makes it easily configurable into any size inverter system, from 200 kVA up to 3.0 MVA capacity. The two operating strategies described below contribute to the system’s reliability and efficiency the most.
Increased longevity via intelligent cycling of inverters | Running fatigue is measured based on the inverter running time. By running the system as a rotating string of inverters, the overall system longevity is increased within the fans’ and capacitors’ limited lifetime (Fig. 4).
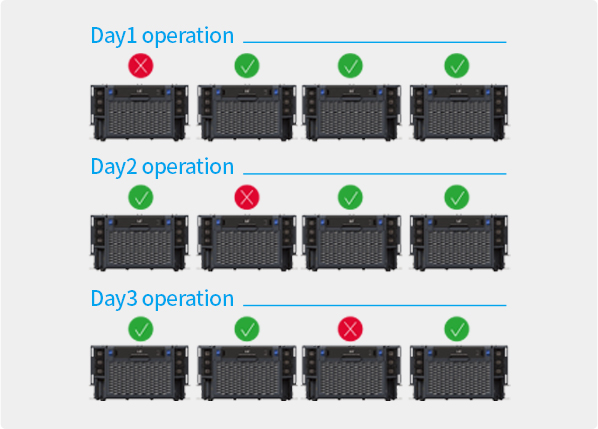
Optimized efficiency for low power mode | The system’s efficiency is enhanced by operating each inverter separately as per the load factor. Therefore, in low load conditions, the system’s efficiency is improved by reducing the number of inverters actively running (Fig. 5).
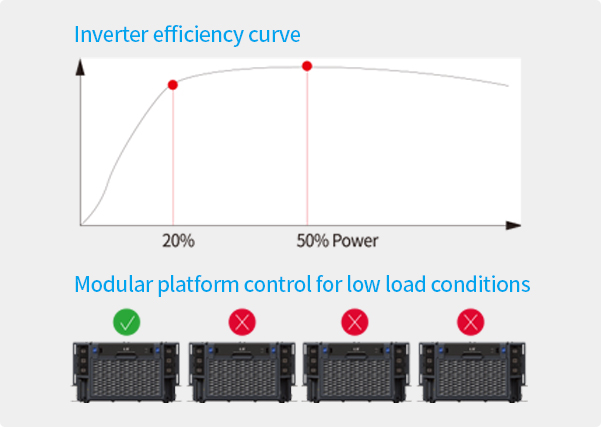
Plans | What would be your next steps?
In the future, we plan to utilize the Typhoon HIL devices even more, especially for improving our development process, as well as for improving our competitive advantage.
These devices are well optimized for the power electronics sector, and we plan to use them to develop single products within the ESS application domain as well as to apply them to a wide range of microgrid applications.
Credits
Author | Debora Santo
Visuals | Karl Mickei
Editor | Debora Santo