Communication will make or break the new grid.
Why is communication potentially the biggest roadblock to a large-scale, smart, decentralized, digitalized grid? Can you imagine wanting to text a friend from your Apple iPhone and not being able to do so because she was using a Samsung Galaxy? Or can you imagine having to install driver software every time you wanted to use your USB memory stick on a different computer? Life would be hell on earth and our digital world would grind to a standstill, right? Of course, these scenarios are figments of (nightmarish) imagination.
Or are they? Unfortunately, the landscape of communication standardization of distributed energy devices (DERs) is essentially nonexistent for the vast majority of DERs that rely on MODBUS. Since its launch in 1979, MODBUS has established itself as a de-facto standard communication protocol for all types of industrial equipment and continues to live on in millions of MODBUS devices that make our industrial civilization possible and our grid operational. Even though most DERs support the same communication protocol – MODBUS – they cannot really “talk” to each other, in the same way, that an IR remote from Sony and an IR remote from Panasonic cannot control the other company’s device despite using the same IR LED and chip.
Mostly, it is about MODBUS…
While MODBUS is a well-established standard for communication across many DER devices, it only standardizes the way messages are organized and transmitted, not the messages themselves. Considering this, trying to integrate devices based on MODBUS support alone is comparable to assuming a group of people can communicate successfully by agreeing to use words, but still allowing everyone to speak in their own language. In practice, this means that the MODBUS message for monitoring the active power output of, say, an SMA solar inverter will be completely different from the MODBUS message used for the very same purpose in a Kostal inverter. Worse still, the same MODBUS message can have completely different effects across different manufacturers; one manufacturer’s inverter may use a message to curtail the output of the inverter to a pre-specified set point, but in another manufacturer’s inverter the same message will switch the inverter off. Sometimes, even the same manufacturer decides to change the “meaning” of MODBUS messages from one DER generation to another.
…but the solutions for MODBUS issues can create other problems.
Some modern communication protocols, such as MODBUS SunSpec, OPC UA, IEC 61850, and OCPP solve the MODBUS message interoperability problem by creating a whole new communication protocol interoperability problem. Each of these protocols could be thought of as a different human language, and a device that “speaks” one protocol (e.g., a battery storage system that uses OPC UA) cannot “talk” to another device that “speaks” another protocol (e.g., an EV charger that uses OCPP). Just as multiple languages require either translation or multilingualism to facilitate useful communication, multiple DER control protocols require the same: error-free translation among protocols or full support for multiple protocols in a single device. Both of these are vanishingly rare or fundamentally nonexistent among even the most current and top-of-the-range DERs and the supervisory control systems that they communicate with.
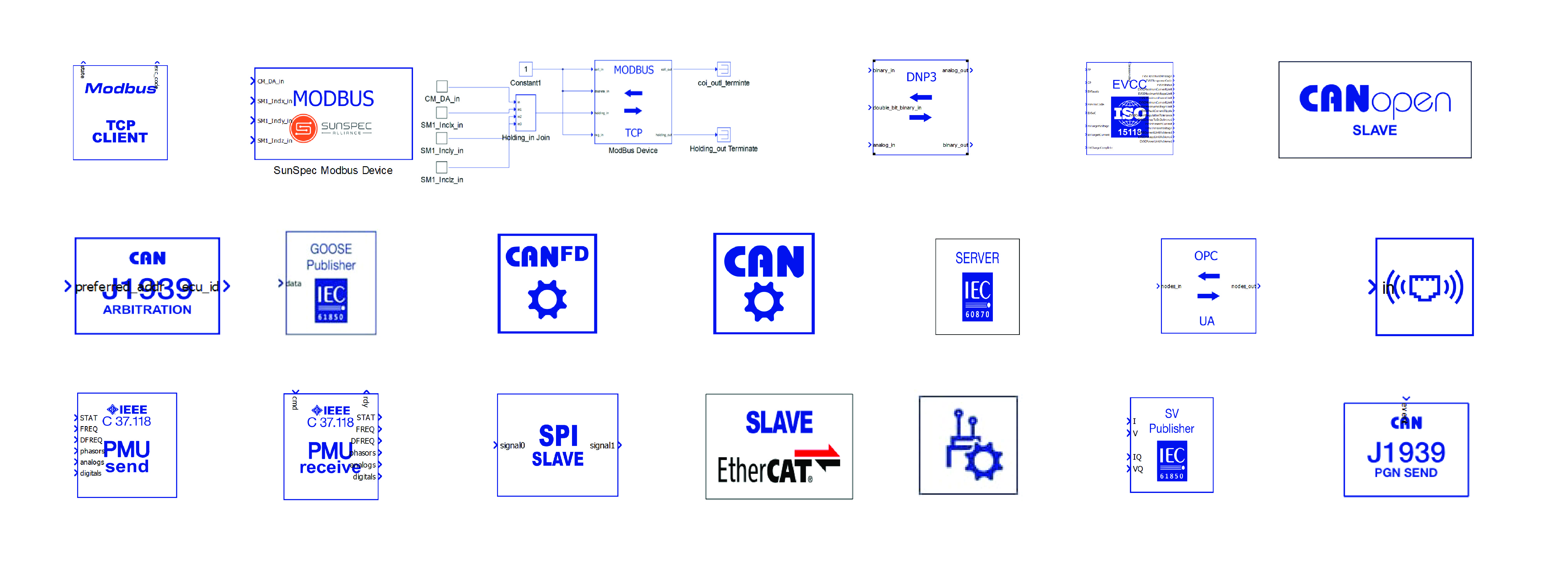
In short, communication is the main roadblock to a smart, decentralized, and digitalized grid since the DERs cannot “talk” to each other, either because of non-standardized MODBUS messages or because of various mutually “unintelligible” protocols. It should be noted that this situation developed through no fault of the device manufacturers, but due to a lack of initiative by governments and international energy organizations to fully standardize DER communication in the same way as was done for ICT.
What can help solve the DER communication problem today?
Instead of simply waiting for governments to align on a standardized form of DER communication, there is a simple solution today to allow different grid actors and DERs to communicate, coordinate, and synchronize their behaviors. This solution is HIL Compatible in combination with the model-based systems engineering methodology of the Microgrid Testbed. This combination not only helps solve the communication challenge, but is also green, safe, efficient, and scalable while supporting rapid grid modernization; accelerating the timeline for achieving agreed-on CO2 emission reduction targets.
Models enable scalability and rapid solving of communication problems.
The model-based hardware-in-the-loop (HIL) approach addresses this problem by combining high-fidelity mathematical models with actual MODBUS register maps, CANbus, IEC61850, and other communication modelling components prior to system deployment. This way, engineers can emulate the behavior of DERs in the power grid they are connected to in real time using, crucially, the same messages they would use with a physical device.
This approach allows for faster and more accurate decision-making, as well as the ability to test and optimize communication and control strategies in the domain of the emulated model, without the dangers of implementing controls on the actual devices and system. Every single monitoring and command message can be tested, and its operation verified virtually, including any cases of blackouts, phase losses, short circuits, etc., to ensure that the microgrid or a specific DER works in all scenarios. Furthermore, this approach enables engineers to identify and address potential interoperability issues and compatibility problems across various DERs earlier in the design process, and way ahead of commissioning. Test results can give critical stakeholders the confidence that devices are set up to function correctly and effectively communicate with each other and the power grid from the moment they are connected in the field.
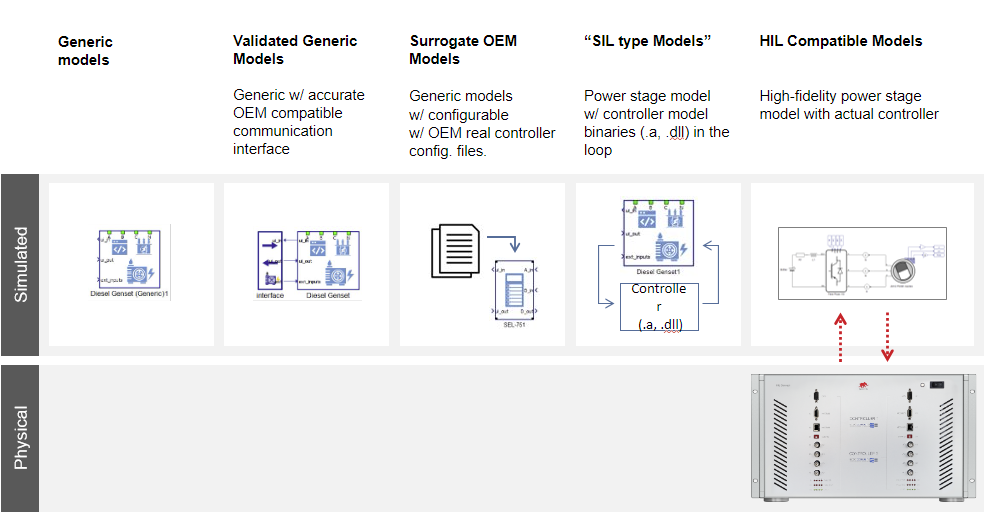
HIL Compatible de-risks deployment and ensures unparalleled speed of integration.
HIL Compatible is a combination of a hardware controller (e.g., an OEM solar inverter controller and its software), and a real-time compatible smart model of the hardware to be controlled. This smart model typically comprises a Typhoon HIL SCADA panel, MODBUS or other communication protocol map, and a model of the power stage, among others. When compared with the model-based hardware-in-the-loop approach, HIL Compatible provides an order-of-magnitude higher fidelity over a modelled controller, since digital integration is based on a physical DER controller using real communication messages (MODBUS or otherwise) at safe power levels. As such, HIL Compatible is an integration dream-come-true for both OEMs and system integrators, because it facilitates seamless integration of devices in various renewable developments, microgrids, or even virtual power plants. Additionally, HIL Compatible is a great way for utilities to qualify new devices or even entire vendors/OEMs.
From the point of view of OEMs and/or DER manufacturers, if a part or all of the product portfolio is in HIL Compatible format, integrators can use them to digitally prepare and integrate their DERs in new projects, ranging from small PV powerplants to entire microgrids comprising of PV, battery storage, wind, gensets, and protection relays. In other words, an OEM/DER manufacturer who provides their portfolio as HIL Compatible, makes it easier for integrators to select and deploy their products, as the integrator can easily use a Microgrid Testbed and HIL Compatible DERs to resolve operational issues in advance and simply push the configuration from the testbed to actual devices. This can reduce the commissioning time for new DER projects by a factor of three or even more, as interoperability and communication issues represent one of the most common causes of delays in commissioning.
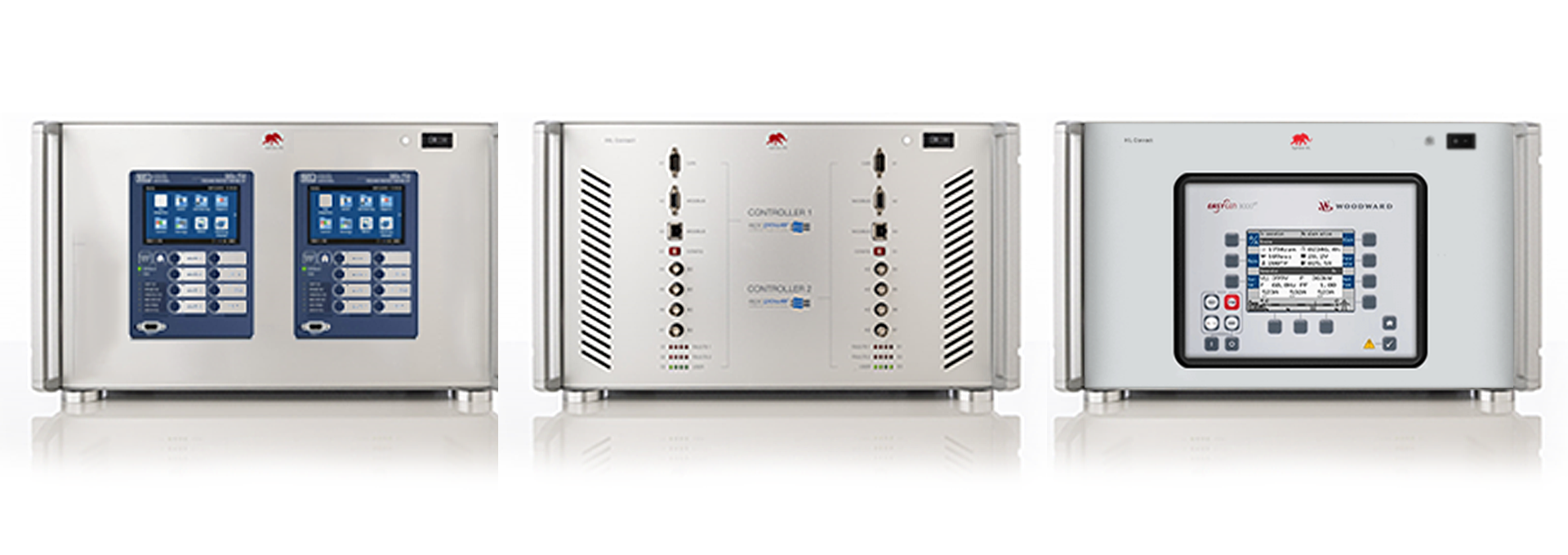
A perfect fit for both the traditional and decentralized approach
The combination of a model-based hardware-in-the-loop approach and HIL Compatible is well fitted to address DER communication issues in both centralized and distributed control systems. Having models and HIL Compatible devices with all relevant communication protocols and maps for all relevant equipment prior to deployment gives more time for integrators, microgrid operators, utilities, and virtual power plant managers to focus on operational algorithms, decision trees, and identifying the optimal control actions without worrying about communication and interoperability issues down the road. Furthermore, this approach provides an excellent way for companies with a wide portfolio of diverse DERs (e.g., utilities, aggregators, virtual power plants, etc.) to qualify new suppliers or new devices from existing suppliers: a model or a HIL Compatible device can be thoroughly tested in a HIL Microgrid Testbed in all operating conditions, including faults, in combination with the previously qualified and “trusted” DERs.
Solve communication problems with HIL Compatible and model-based HIL
The biggest advantage of the model-based hardware-in-the-loop approach paired with HIL Compatible devices is that it enables solving interoperability of smart grid-tied DERs early in the development of new microgrids, installations, systems, or systems of systems, whether the devices use MODBUS, more recent communication protocols such as OPC UA, or a combination of them. Using the same protocols and communication messages in the Microgrid Testbed as in the physical devices allows for testing and simulation of device communication and control systems in a controlled and safe environment, before being deployed in the actual system. Furthermore, this enables communication set-up from DER models in the Microgrid Testbed to be pushed to physical devices, cutting commissioning time by several orders of magnitude. This approach enables engineers to identify and address potential interoperability issues and compatibility problems early in the development process so that the main engineering efforts can be used for testing and optimizing control algorithms and strategies – not fixing communication issues – which further improves the overall performance and reliability of any kind of a smart grid installation. Finally, this approach is an excellent choice for pre-qualifying OEM suppliers, enabling both integrators and OEMs a completely new level of efficiency and confidence in delivering projects on time.
Credits
Text | Aleksandar Kavgic
Visuals | Karl Mickei, Milica Obradovic
Editors | Sergio Costa, Debora Santo