Single Phase Three Winding Transformer
Description of the Single Phase Three Winding Transformer component in Schematic Editor
Component Description
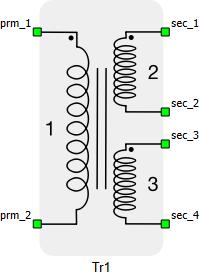
The Single Phase Three Winding Transformer component models three coupled windings on the same core. The magnetization inductance Lm can be linear or with saturation, it is modeled on the primary side of the transformer. Core losses are modeled as Rm resistance located on the primary side of the transformer. Also, it is possible to neglect Lm and Rm by selecting Lm/Rm neglected in the Core model property. Finally, Hysteresis can also be simulated for slower dynamics. For more information, please refer to the Core model section.
A schematic block diagram of the single-phase three-winding transformer block with the corresponding component arrangement and naming is shown in Figure 2.
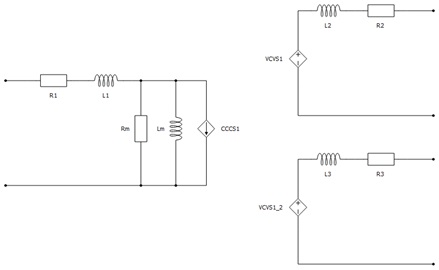
Embedded coupling
There are two possible options for embedded coupling in the Single Phase Three Winding Transformer: Ideal Transformer based coupling and TLM coupling. Also, it is possible to insert embedded coupling between winding 1 and 2, 1 and 3, and both of them.
Ideal Transformer Embedded coupling type is ignored in TyphoonSim and will not affect TyphoonSim simulation at all.
- TLM Embedded coupling type will be replaced with a corresponding inductor in TyphoonSim.
If Embedded coupling is set to Ideal Transformer, Ideal Transformer based coupling will be placed between two windings of transformer.
Visual representations of circuit division among standard processing cores are given in:
- Figure 3 when Embedded coupling 1-3 is set to Ideal Transformer;
- Figure 4 when both Embedded coupling 1-2 and Embedded coupling 1-3 are set to Ideal Transformer.
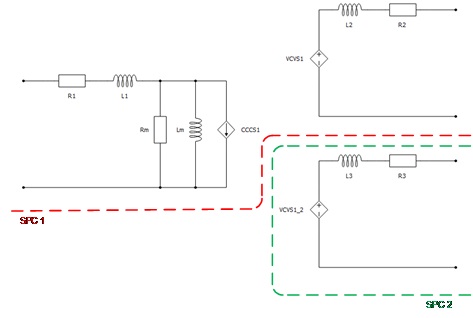
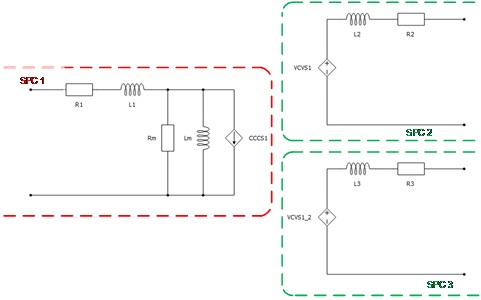
If Embedded coupling is set to TLM, a secondary winding inductor will be replaced with the TLM coupling component. Inductance will be divided between coupling and embedded inductors (inductors will be hidden in the TLM). The TLM to embedded inductors ratio can be determined by the compiler, but it can also be specified explicitly. If the Automatic option is selected, the ratio will be determined by the discretization method. If the Manual option is selected, the ratio can be explicitly set to meet user requirements. For more information on TLM couplings, please refer to Core couplings - TLM.
Visual representations of circuit division among standard processing cores are given in:
- Figure 5 when Embedded coupling 1-3 is set to TLM;
- Figure 6 when both Embedded coupling 1-2 and Embedded coupling 1-3 are set to TLM.
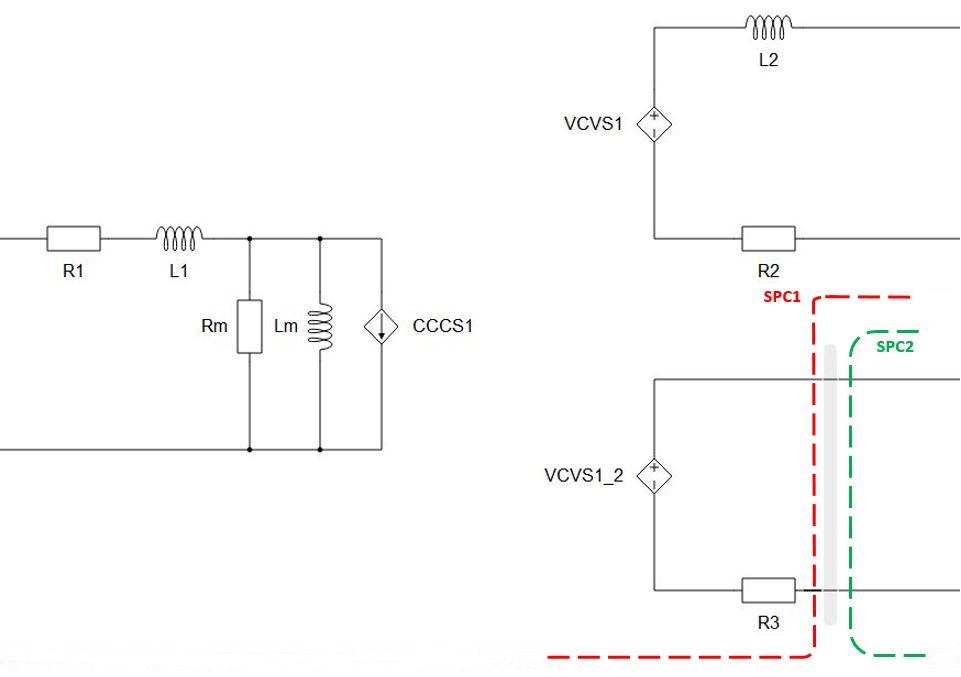
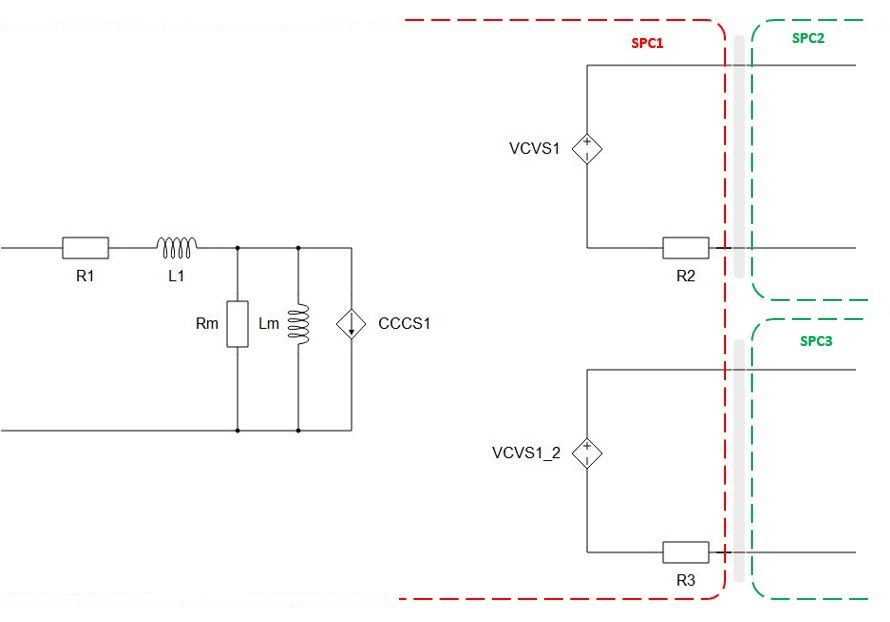
Hysteresis effects
Simulating hysteresis effects requires signal processing implementation. Therefore, an execution rate for hysteresis simulation must be specified. To capture this effect for an arbitrary dynamic signal, its period should be at least 20 times faster than the execution rate of hysteresis sampling, defined in Execution rate. Hysteresis is further defined through three lists/arrays which have different labels depending on the type of transformer or nonlinear inductor as shown in Figure 7.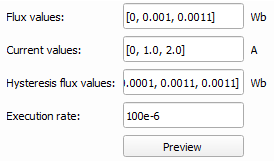
To properly define hysteresis, the data value for both Flux values and Hysteresis flux values must be specified for the zero current data-point, which means that the first value of Current values and Flux values lists/arrays must be 0, and that the first value of the Hysteresis flux values list/array must be the remanent flux value. Secondly, all three of these properties must have the same number of elements and all three must be monotonically non-decreasing lists/arrays. Hysteresis flux values must have at least one element that is higher in value than the corresponding element in the Flux values list, followed by at least one element that has the same value as the corresponding element in Flux values. The first common element for Hysteresis flux values and Flux values is defined as the Hysteresis upper curve threshold.
Figure 8 demonstrates an example of properly defined parameter values using the settings below.
Flux values [Wb]: [0, 0.004, 0.008, 0.011, 0.013, 0.014, 0.0145, 0.015]
Current values [A]: [0, 1, 2, 3, 4, 5, 6, 7]
Hysteresis flux values [Wb]: [0.004, 0.007, 0.01, 0.012, 0.0135, 0.0141, 0.0145, 0.015]
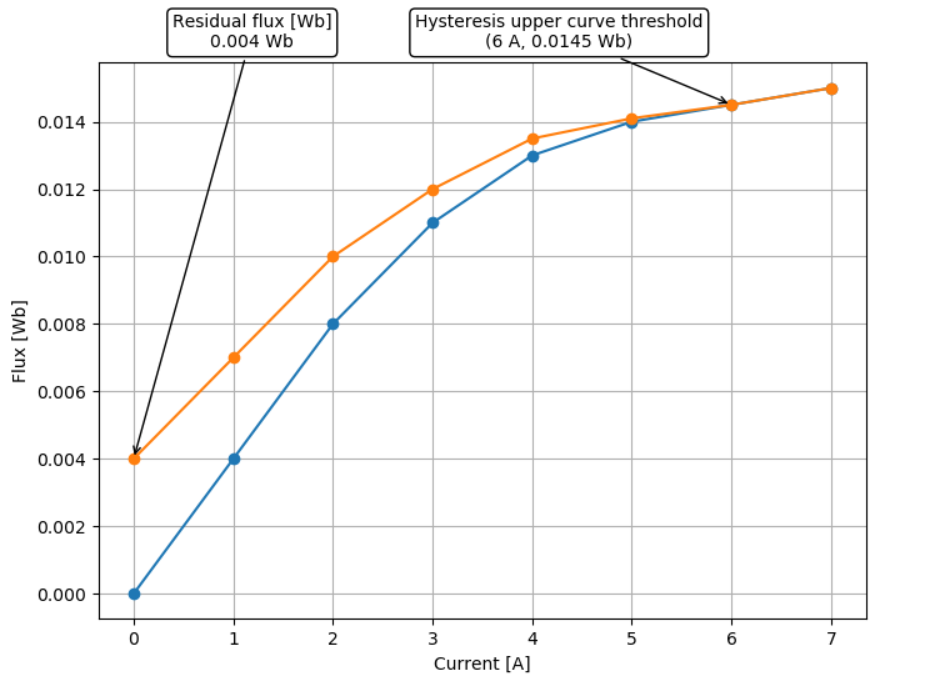
Clicking the Preview button will validate the hysteresis parameters, but only if they are defined directly in the respective property fields and not if they are defined through the namespace. After validation, the Hysteresis curve will be extended, showing the expected simulation hysteresis curve as shown in Figure 9.

When the simulated flux value surpasses the Hysteresis upper curve threshold, the upper curve becomes the trajectory for the flux-current set-points and stays that way until the next trigger event. When the simulated flux value falls bellow the Hysteresis bottom curve threshold, the bottom curve becomes the trajectory for the flux-current set-points and stays that way until the next trigger event. When the simulation is first started, the original curve is a reference, until the next trigger event. A way to disable hysteresis and return the reference curve to the original magnetization curve during runtime, is to set the scada input named demagnetize_scada_in to 1. To re-enable the hysteresis upper and bottom curve, set the scada input demagnetize_scada_in to 0. Flux demagnetization to the reference curve is not supported in TyphoonSim yet.
Ports
- prm_1 (electrical)
- Primary winding port 1.
- prm_2 (electrical)
- Primary winding port 2.
- sec_1 (electrical)
- Secondary winding port 1.
- sec_2 (electrical)
- Secondary winding port 2.
- sec_3 (electrical)
- Secondary winding port 3.
- sec_4 (electrical)
- Secondary winding port 4.
General (Tab)
- Input parameters
- Specifies parameters format (SI or pu).
- Sn
- Available if Input parameters is set to pu.
- Nominal Power of the transformer [VA].
- fn
- Available if Input parameters is set to pu.
- Nominal frequency [Hz].
- V1
- Rated voltage of winding 1 (primary) [Vrms].
- V2
- Rated voltage of winding 2 [Vrms].
- V3
- Rated voltage of winding 3 [Vrms].
- R1
- Available if Input parameters is set to SI.
- Resistance of winding 1 (primary) [Ω].
- r1
- Available if Input parameters is set to pu.
- Resistance of winding 1 (primary) [p.u.].
- L1
- Available if Input parameters is set to SI.
- Leakage inductance of winding 1 (primary) [H].
- l1
- Available if Input parameters is set to pu.
- Leakage inductance of winding 1 (primary) [pu].
- I1
- Available if Input parameters is set to SI.
- Initial current of winding 1 (primary) [A].
- i1
- Available if Input parameters is set to pu.
- Initial current of winding 1 (primary) [pu].
- R2
- Available if Input parameters is set to SI.
- Resistance of winding 2 [Ω].
- r2
- Available if Input parameters is set to pu.
- Resistance of winding 2 [pu].
- L2
- Available if Input parameters is set to SI.
- Leakage inductance of winding 2 [H].
- l2
- Available if Input parameters is set to pu.
- Leakage inductance of winding 2 [pu].
- I2
- Available if Input parameters is set to SI.
- Initial current of winding 2 [A].
- i2
- Available if Input parameters is set to pu.
- Initial current of winding 2 [pu].
- R3
- Available if Input parameters is set to SI.
- Resistance of winding 3 [Ω].
- r3
- Available if Input parameters is set to pu.
- Resistance of winding 3 [pu].
- L3
- Available if Input parameters is set to SI.
- Leakage inductance of winding 3 [H].
- l3
- Available if Input parameters is set to pu.
- Leakage inductance of winding 3 [pu].
- I3
- Available if Input parameters is set to SI.
- Initial current of winding 3 [A].
- i3
- Available if Input parameters is set to pu.
- Initial current of winding 3 [pu].
- Core model
- Selects transformer core model implementation.
- Several levels of model fidelity are available - Linear, Non-Linear, Rm/Lm neglected, or Hysteresis.
- Rm
- Available if Input parameters is set to SI and Core model is set to Linear, Non-Linear, or Hysteresis.
- Resistance representing core losses [Ω].
- rm
- Available if Input parameters is set to pu and Core model is set to Linear, Non-Linear or Hysteresis.
- Resistance representing core losses [pu].
- Lm
- Available if Input parameters is set to SI and Core model is set to Linear.
- Magnetization inductance [H].
- lm
- Available if Input parameters is set to pu and Core model is set to Linear.
- Magnetization inductance [pu].
- Flux values
- Available if Core model is set to Non-Linear or Hysteresis.
- List of magnetic flux values [Wb] or [pu].
- Current values
- Available if Core model is set to Non-Linear or Hysteresis.
- List of current values [A] or [pu].
- Hysteresis flux
- Available if Core model is set to Hysteresis.
- List of hysteresis flux values [Wb] or [pu].
- Execution rate
- Execution rate for hysteresis effect simulation.
Coupling (Tab)
Ideal Transformer Embedded coupling type is ignored in TyphoonSim and will not affect TyphoonSim simulation at all.
- TLM Embedded coupling type will be replaced with a corresponding inductor in TyphoonSim.
- Embedded coupling 1-2
- Embedded coupling option - inserts a coupling component between winding 1 and 2 - can be set to Ideal Transformer, TLM or None.
- TLM 1-2/Embedded components ratio
- Available if Embedded coupling 1-2 is set to TLM.
- Defines how coupling to embedded inductors ratio will be calculated (automatic or manual). Related to coupling between winding 1 and 2.
- Embedded coupling 1-3
- Embedded coupling option - inserts a coupling component between winding 1 and 3 - can be set to Ideal Transformer, TLM or None.
- TLM 1-3/Embedded components ratio
- Available if Embedded coupling 1-3 is set to TLM.
- Defines how coupling to embedded inductors ratio will be calculated (automatic or manual). Related to coupling between winding 1 and 3.
- Type of coupling element
- Available if corresponding Embedded coupling is set to Ideal Transformer or TLM.
- Defines whether the inserted coupling element is a core or a device coupling.
- Device coupling is available if corresponding Embedded coupling is set to Ideal Transformer for all HIL devices except HIL402.
- Ratio
- Available if corresponding Embedded coupling is set to TLM and TLM/Embedded components ratio is set to Manual.
- Specifies coupling to embedded inductors ratio.