Three Phase Permanent Magnet Synchronous Machine (JMAG)
Description of the Three Phase Permanent Magnet Synchronous Machine JMAG component in Schematic Editor.
A, B, and C are stator winding terminals. The stator winding uses the current source interface.
JMAG-RT data files
JMAG is a simulation software for the development and design of electrical devices, mainly electrical machines. JMAG software accurately analyzes a wide range of physical phenomena that includes complicated geometry, various material properties, and the heat and structure at the center of electromagnetic fields.
JMAG-RT is a tool that generates high fidelity plant models. These models are based on FEA results and can be calculated quickly while retaining high accuracy. The models can be used in system level simulations to provide a more accurate representation of a simulated electromagnetic device. From the 2020.2 version of Typhoon HIL Control Center, simulation of certain JMAG-RT generated machine models is supported.
The electrical parameters of the machine model are defined using an .rtt file. A valid .rtt file that contains the LdLq and/or Flux integral model types needs to be generated in order to use this feature. In addition to the appropriate model type(s), the .rtt file must contain the number of poles. The inertia of the machine should be designated in the component parameters, under the Mechanical (Tab).
- LdLq (table)
- Flux integral
- Spatial harmonic
By default, the stator winding resistance is read from the .rtt file. If necessary, it can be set manually after checking the Set resistance manually box.
The Flux integral type allows for correction factors to adjust simulation results. The correction factors are read from the .rtt file and applied to the simulation model. These factors affect inductances, magnetic fluxes, currents, and torque.
The Flux integral type also allows for losses calculation. The chosen .rtt file needs to contain the eddy current and hysteresis loss lookup tables in order to use this feature. Two types of losses are calculated - eddy current losses and hysteresis losses. These can be selected among the output signals in the "Output" tab.
Ports
- A (electrical)
- Stator winding phase A port.
- B (electrical)
- Stator winding phase B port.
- C (electrical)
- Stator winding phase C port.
- in
- Available if Model Load source is selected
Electrical (Tab)
- RT data file path
- Path to the .rtt file
- Accuracy Type
- Accuracy type - it can be LdLq(table) or Flux integral
- Set resistance manually
- Enables setting the value of stator resistance manually
- Rs
- Available if Set resistance manually is enabled
- Stator phase resistance [Ω]
- Use correction coefficients
- Available if Accuracy type is set to Flux integral
- Enables use of correction factors to adjust simulation results
- Losses calculation
- Available if Accuracy type is set to Flux integral and Use correction coefficients is set to False
- Enables losses calculation. Currently supported losses are eddy current and hysteresis losses
Losses calculation is not supported in TyphoonSim yet
- Low-pass filter cut-off frequency
- Available if Losses calculation is set to True
- Low-pass filter cut-off frequency used to filter out high frequency components in the induced voltage, when calculating losses [Hz]
Mechanical (Tab)
- Jm
- Combined rotor and load moment of inertia [kgm2]
- Friction coefficient
- Machine viscous friction coefficient [Nms]
-
Star/delta
- Stator winding connection (star or delta)
Stator winding connection option is not supported in TyphoonSim. Changing its value will not affect TyphoonSim simulation at all.
- Unconstrained mechanical angle
- Limiting mechanical angle between 0 and 2π
Load (Tab)
- Load source
- Load source can be set from SCADA/external or from model (in model case, one signal processing input will appear).
- In TyphoonSim, if SCADA/external is chosen as Load source, analog signals are read from the internal virtual IO bus. Hence, if some signal is sent to analog ouput 1, it will appear on analog input 1.
- External/Model load type
- Load type: torque or speed
- Load ai pin
- Load ai pin for external torque/speed command.
- In real-time/VHIL simulation, Load ai pin represent HIL analog input address for external torque command.
- In TyphoonSim, analog signals are read from the internal virtual IO bus. Hence, if some signal is sent to analog ouput 1, it will appear on analog input 1.
- Available only if SCADA/external is set as Load source.
- Load ai offset
- Assigned offset value to the input signal representing external torque command.
- Available only if SCADA/external is set as Load source.
- Load ai gain
- Assigned gain value to the input signal representing external torque command.
- Available only if SCADA/external is set as Load source.
External load enables you to use an analog input signal from a HIL/TyphoonSim (internal virtual IO bus in TyphoonSim) analog channel with the load_ai_pin address as an external torque/speed load, and to assign offset (V) and gain (Nm/V) to the input signal, according to the formula:
Feedback (Tab)
- Encoder ppr
- Incremental encoder number of pulses per revolution
- Encoder Z pulse length
- Z digital signal pulse length in periods. Can be Quarter length or Full period (default)
- Resolver pole pairs
- Resolver number of pole pairs
- Resolver carrier source
- Resolver carrier signal source selection (internal or external)
- Resolver carrier frequency
- Resolver carrier signal frequency (internal carrier) [Hz]
- Available only if the Resolver carrier source property is set to internal
- External resolver carrier source type
- External resolver carrier signal source type selection (single ended or differential)
- Available only if the Resolver carrier source property is set to external
- Resolver ai pin 1
- Resolver carrier input channel 1 address (external carrier)
- Available only if the Resolver carrier source property is set to external
- In TyphoonSim, analog signals are read from the internal virtual IO bus. Hence, if some signal is sent to analog ouput 1, it will appear on analog input 1.
- Resolver ai pin 2
- Resolver carrier input channel 2 address (external carrier)
- Available only if the Resolver carrier source property is set to externaland External resolver carrier source type property is set to differential
- In TyphoonSim, analog signals are read from the internal virtual IO bus. Hence, if some signal is sent to analog ouput 1, it will appear on analog input 1.
- Resolver ai offset
- Resolver carrier input channel offset (external carrier)
- Available only if the Resolver carrier source property is set to external
- In TyphoonSim, analog signals are read from the internal virtual IO bus. Hence, if some signal is sent to analog ouput 1, it will appear on analog input 1.
- Resolver ai gain
- Resolver carrier input channel gain (external carrier)
- Available only if the Resolver carrier source property is set to external
- In TyphoonSim, analog signals are read from the internal virtual IO bus. Hence, if some signal is sent to analog ouput 1, it will appear on analog input 1.
- Absolute encoder protocol
- Standardized protocol providing the absolute machine encoder position.
Absolute encoder protocol is ignored in TyphoonSim. Changing its value will not affect TyphoonSim simulation at all.
- Singleturn bits
- Number of machine absolute encoder singleturn bits.
- Available only if Absolute encoder protocol is not None.
Absolute encoder protocol is ignored in TyphoonSim. Changing its value will not affect TyphoonSim simulation at all.
- Enable multiturn
- Enables multiturn absolute encoder support.
- Available only if Absolute encoder protocol is not None.
Absolute encoder protocol is ignored in TyphoonSim. Changing its value will not affect TyphoonSim simulation at all.
- Multiturn bits
- Number of machine absolute encoder multiturn bits.
- Available only if Enable multiturn is checked.
Absolute encoder protocol is ignored in TyphoonSim. Changing its value will not affect TyphoonSim simulation at all.
- EnDat/SSI/BiSS clock DI pin
- Clock digital input pin for the chosen absolute encoder protocol type.
- Available only if Absolute encoder protocol is not None.
Absolute encoder protocol is ignored in TyphoonSim. Changing its value will not affect TyphoonSim simulation at all.
- Clock DI logic
- Clock DI pin logic: active high/active low.
- Available only if Absolute encoder protocol is not None.
Absolute encoder protocol is ignored in TyphoonSim. Changing its value will not affect TyphoonSim simulation at all.
- EnDat data DI pin
- EnDat data digital input pin.
- Available only if Absolute encoder protocol is EnDat.
Absolute encoder protocol is ignored in TyphoonSim. Changing its value will not affect TyphoonSim simulation at all.
- Data DI logic
- EnDat data DI pin logic: active high/active low.
- Available only if Absolute encoder protocol is EnDat.
Absolute encoder protocol is ignored in TyphoonSim. Changing its value will not affect TyphoonSim simulation at all.
If an external resolver carrier source is selected, the source signal type can be set as either single ended or differential. The single ended external resolver carrier source type enables use of an analog input signal from the HIL/TyphoonSim (internal virtual IO bus in TyphoonSim) analog channel with the res_ai_pin_1 address as the external carrier source. Additionally, offset (V) and gain (V/V) values can be assigned to the input signal, according to the formula:
The differential external resolver carrier source type enables use of two analog input signals from the HIL/TyphoonSim (internal virtual IO bus in TyphoonSim) analog channels with the res_ai_pin_1 and the res_ai_pin_2 addresses. Analog signals from these HIL/TyphoonSim (internal virtual IO bus in TyphoonSim) analog inputs are subtracted, and the resulting signal is used as the external differential carrier source. Additionally, offset (V) and gain (V/V) values can be assigned to the input signal (similarly to the single ended case), according to the formula:
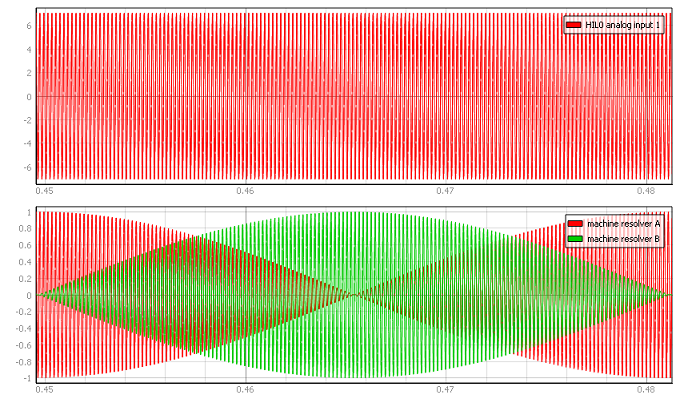
The following expression must hold in order to properly generate the encoder signals:
symbol | description |
---|---|
enc_ppr | Encoder number of pulses per revolution |
fm | Rotor mechanical frequency [Hz] |
Ts | Simulation time step [s] |
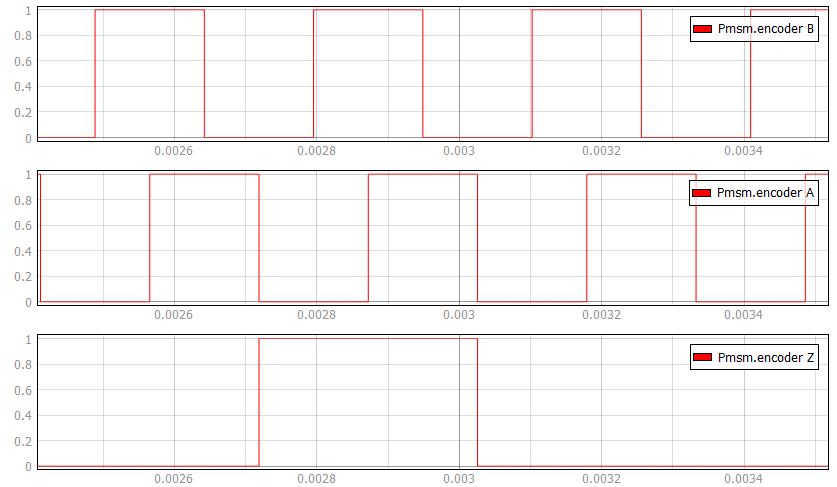
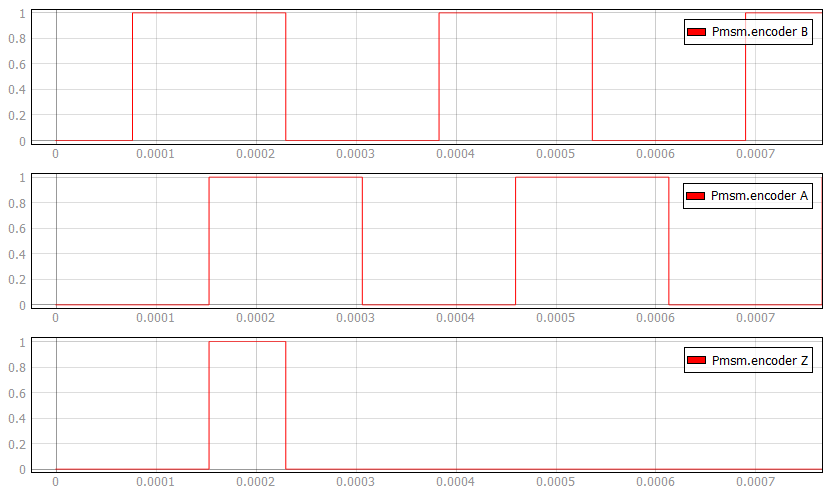
Advanced (Tab)
- Theta_ab
- Position of the stationary αβ reference frame, in respect to the stator phase a axis [rad]
- Field Input
- Physical quantity applied to the field winding - voltage or current. It refers to the rotor-side.
In order for the input field current to be referred to the stator parameter, Ns/Nfd in the Electrical Tab should be set to
Note: If field input is defined as current, the field winding equation is removed from the mathematical model. Instead, the field input current is used as the model's input. There is no support for 2 q-axis damper windings with current input as of yet. For linear machine models, you can choose whether to apply voltage or current to the field winding. Nonlinear machine models only allows voltage as a field input.Field Input option is not supported in TyphoonSim. Changing its value will not affect TyphoonSim simulation at all
The machine model output variables (currents, voltages and fluxes) can be observed from a stationary reference frame. There are two widely used approaches in electrical machine modeling: in the first, the alpha axis of the stationary reference frame lags by 90 degrees in regard to the stator phase a axis (used by default, and indicated in a) Figure 5. In the second one, the alpha axis is aligned with the stator phase a axis (indicated in b) Figure 5. The user can select between these two situations.
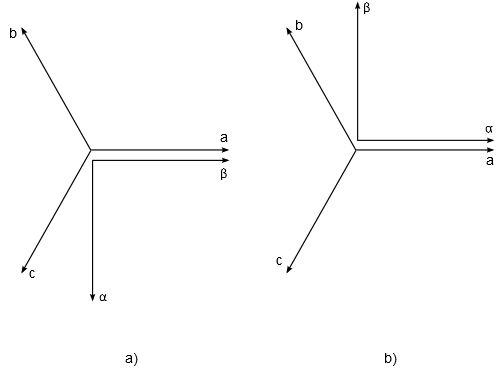
It is important to know the value of Theta_ab when the rotor position feedback is necessary. As an example, if a model uses the mechanical angle as a feedback signal and feeds it to one of the abc to dq, alpha beta to dq, dq to abc, or dq to alpha beta transformation blocks, the same transformation angle offset value should be used in both components to ensure the expected simulation results.
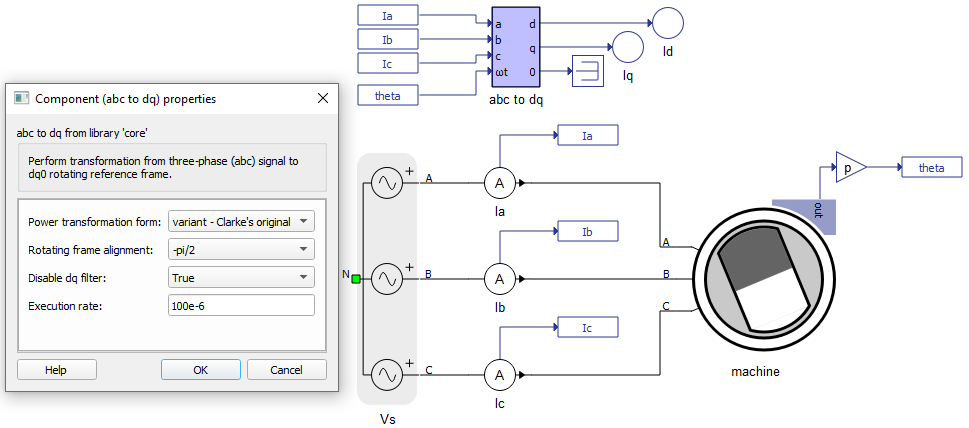
Snubber (Tab)
- Rsnb stator
- Stator snubber resistance value [Ω]
All machines with current source based circuit interfaces have the Snubber tab in the properties window where the value of snubber resistance can be set. Snubbers are necessary in the cases when an inverter or a contactor is directly connected to the machine terminals. This value can be set to infinite (inf), but it is not recommended when a machine is directly connected to the inverter since there will be a current source directly connected to an open switch. In this case, one of each switch pairs S1 and S2, S3 and S4, and S5 and S6 will be forced closed by the circuit solver in order to avoid the topological conflicts. On the other hand, with finite snubber values, there's always a path for the currents Ia and Ib, so all inverter switches can be open in this case. Circuit representations of this circuit without and with snubber resistors are shown in Figure 7 and Figure 8 respectively. Snubbers are connected across the current sources.
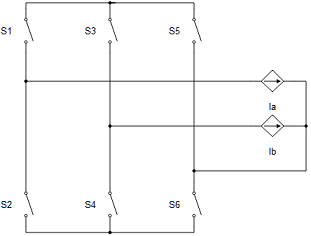
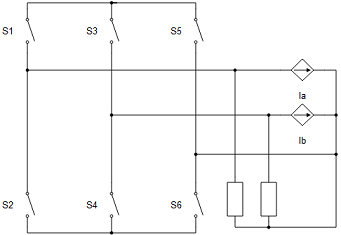
Output (Tab)
This block tab enables a single, vectorized signal output from the machine. The output vector contains selected machine mechanical and/or electrical variables in the same order as listed in this tab.
- Execution rate
- Signal processing output execution rate [s]
- Electrical torque
- Machine electrical torque [Nm]
- Mechanical speed
- Machine mechanical angular speed [rad/s]
- Mechanical angle
- Machine mechanical angle [rad]
- Stator alpha axis current
- Alpha axis component of the stator current [A]
- Stator beta axis current
- Beta axis component of the stator current [A]
- Stator d-axis current
- Direct axis component of the stator current [A]
- Stator q-axis current
- Quadrature axis component of the stator current [A]
- Stator alpha axis flux
- Alpha axis component of the stator flux [Wb]
- Stator beta axis flux
- Beta axis component of the stator flux [Wb]
- Stator d-axis flux
- Direct axis component of the stator flux [Wb]
- Stator q-axis flux
- Quadrature axis component of the stator flux [Wb]
- Eddy current losses
- Available if Accuracy Type is set to Flux integral and Losses calculation is enabled
- Eddy current losses [W]
Eddy current losses output is not supported in Typhoonsim yet.
- Hysteresis losses
- Available if Accuracy Type is set to Flux integral and Losses calculation is enabled
- Hysteresis losses [W]
Hysteresis losses output is not supported in Typhoonsim yet.
Extras (Tab)
The Extras tab gives you the opportunity to set Signal Access Management for the component.
- Public - Components marked as public expose their signals on all levels.
- Protected - Components marked as protected will hide their signals to components outside of their first locked parent component.
- Inherit - Components marked as inherit will take the nearest parent 'signal_access' property value that is set to a value other than inherit.